Elastic-plastic structure damping support
A structural damping and elastoplastic technology, applied to bridge parts, bridge materials, bridges, etc., can solve the problems of fatigue, energy consumption and poor limit effect, and achieve the effect of maintaining stability, convenient maintenance and post-earthquake replacement
- Summary
- Abstract
- Description
- Claims
- Application Information
AI Technical Summary
Problems solved by technology
Method used
Image
Examples
Embodiment 1
[0058] A one-way movable elastic-plastic mild steel structure damping support, its structure see Figure 1 to Figure 7 shown, including:
[0059] Supporting module: including the upper top plate 1, spherical cap 5, middle liner 6 and lower bottom plate 9 stacked from top to bottom, wherein, between the upper top plate 1 and the spherical cap 5, between the lower bottom plate 9 and the middle liner 6 Sliding surfaces that move relatively along the bridge direction and the transverse bridge direction are respectively processed, and the spherical cap 5 and the intermediate liner 6 are connected through spherical contact;
[0060] Damping module: including energy-limiting components arranged along the direction of the bridge and along the direction of the bridge, wherein the two ends of the energy-limiting components arranged along the direction of the bridge are respectively connected to the top plate 1 and the spherical cap 5, and along the direction of the bridge The two ends ...
Embodiment 2
[0070] A fixed elastic-plastic structure damping support, its structure see Figure 12-Figure 16 As shown, the difference from Embodiment 1 is that along the direction of the bridge, the upper top plate 1 of the support is replaced by the fourth lug 10 connected by high-strength bolts 23 to the fourth ear plate 20, and the upper limit ring 11 is removed. The two end sides of the limiting ring 11 are fixedly connected with the fourth ear plate 20 and the first ear plate 14 respectively. Simultaneously, pin holes 7 are set up on the forward slideway 15 on the upper top plate 1 and the guide block 3 on the spherical cap 5, and the limited capacity shearing pins 8 are placed in the pin holes 7.
Embodiment 3
[0072] Two-way active elastic-plastic mild steel structure damping bearing, its structure see Figure 17-Figure 20 As shown, the difference from the first embodiment is that along the direction of the bridge, the second lug plate 17 connected by the lower bottom plate of the support 9 through high-strength bolts 23 is replaced by the second limit chute 22, and the middle liner 6 is connected by high-strength bolts 23 The third ear plate 18 is connected, and one end side of the limit ring 11 is provided with a transverse tie rod 21, and the transverse tie rod 21 is snapped into the second limit chute 22 connected with the lower bottom plate, and can slide freely. The other end of 11 is connected to the lug 18 of the intermediate lining. At the same time, remove the pin hole 7 and the limited capacity shear pin 8 on the transverse slideway 16 of the base plate 9 and on the guide block 3 at the bottom of the intermediate liner 6 .
PUM
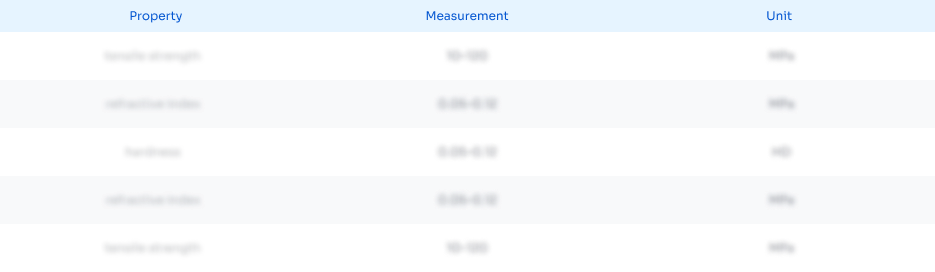
Abstract
Description
Claims
Application Information

- Generate Ideas
- Intellectual Property
- Life Sciences
- Materials
- Tech Scout
- Unparalleled Data Quality
- Higher Quality Content
- 60% Fewer Hallucinations
Browse by: Latest US Patents, China's latest patents, Technical Efficacy Thesaurus, Application Domain, Technology Topic, Popular Technical Reports.
© 2025 PatSnap. All rights reserved.Legal|Privacy policy|Modern Slavery Act Transparency Statement|Sitemap|About US| Contact US: help@patsnap.com