Collimating lens, laser module, depth camera and electronic device
A lens and collimation technology, which is applied in the field of collimation lenses, can solve problems affecting the imaging accuracy of depth images and calculation errors of depth cameras, and achieve the effects of reducing process complexity, ensuring yield, and improving competitiveness
- Summary
- Abstract
- Description
- Claims
- Application Information
AI Technical Summary
Problems solved by technology
Method used
Image
Examples
no. 1 example
[0056] see Figure 1 to Figure 4 , in the collimating lens 11 of the first embodiment, the effective focal length f=4.267mm of the collimating lens 11 when the temperature is -15 degrees (°), and the effective focal length f=4.264mm when the temperature is 60 °; the focal length f The focal length change within the temperature range [-15°, 60°] is within 0.003mm, and it has good temperature change stability.
[0057] The total optical length of the collimating lens 11 (that is, the distance from the object plane S0 to the image side S8 of the fourth lens L4 on the optical axis) TTL=3.400 mm. The numerical aperture NA of the collimator lens 11 is 0.18mm.
[0058] The collimating lens 11 satisfies the following conditions: TTL / f=0.797; f4 / f1=1.572; f4 / f2=-3.368; f4 / f3=0.698; f / R8=-3.416; R1 / R8=-0.813; CT4 / CT2 = 1.847. The collimating lens 11 also meets the conditions of the following table:
[0059] Table I
[0060]
[0061]
[0062] Table 2
[0063]
no. 2 example
[0065] see figure 1 , Figure 5 to Figure 7 , in the collimating lens 11 of the first embodiment, the effective focal length f=3.989mm of the collimating lens 11 when the temperature is -15 degrees (°), and the effective focal length f=3.988mm when the temperature is 60 °; the focal length f When the focal length changes within the temperature range [-15°, 60°] within 0.001mm, it has good temperature change stability.
[0066] The total optical length of the collimating lens 11 (that is, the distance from the object plane S0 to the image side S8 of the fourth lens L4 on the optical axis) TTL=3.295mm. The numerical aperture NA of the collimator lens 11 is 0.18mm.
[0067] The collimating lens 11 satisfies the following conditions: TTL / f=0.826; f4 / f1=1.914; f4 / f2=-3.234; f4 / f3=0.698; f / R8=-3.155; R1 / R8=-0.803; CT4 / CT2 = 1.914. The collimating lens 11 also meets the conditions of the following table:
[0068] table 3
[0069]
[0070] Table 4
[0071]
[0072] see f...
PUM
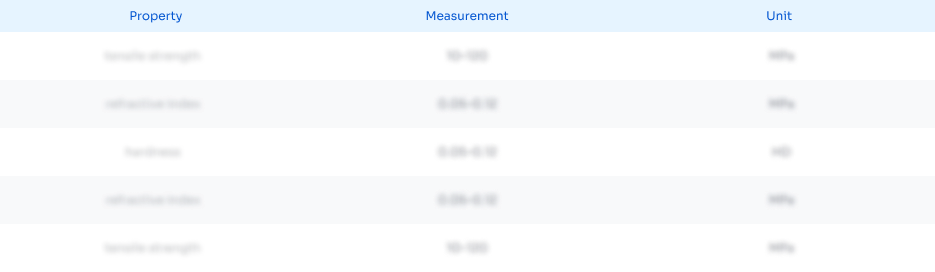
Abstract
Description
Claims
Application Information

- Generate Ideas
- Intellectual Property
- Life Sciences
- Materials
- Tech Scout
- Unparalleled Data Quality
- Higher Quality Content
- 60% Fewer Hallucinations
Browse by: Latest US Patents, China's latest patents, Technical Efficacy Thesaurus, Application Domain, Technology Topic, Popular Technical Reports.
© 2025 PatSnap. All rights reserved.Legal|Privacy policy|Modern Slavery Act Transparency Statement|Sitemap|About US| Contact US: help@patsnap.com