Truss type machine tool feeding and blanking robot system and control method thereof
A robot system, truss-type technology, applied in the direction of program-controlled manipulators, manipulators, manufacturing tools, etc., can solve the problems of continuous positioning and grasping of the feeding tray, and achieve the effect of free switching
- Summary
- Abstract
- Description
- Claims
- Application Information
AI Technical Summary
Problems solved by technology
Method used
Image
Examples
Embodiment Construction
[0028] In order to make the technical problems, technical solutions and advantages to be solved by the present invention clearer, the following will describe in detail with reference to the drawings and specific embodiments.
[0029] The invention provides a truss type machine tool loading and unloading robot system and a control method thereof.
[0030] Such as figure 1 As shown, the system includes a truss robot 1, a feeding tray 3, a feeding tray 4 and a CNC lathe 2, the loading tray 3 and the feeding tray 4 are located between two CNC machine tools 2, and the truss robot 1. The workpiece is transferred between the loading tray 3, the unloading tray 4 and the CNC machine tool 2; the truss robot 1 is composed of a rack and pinion, a reducer, a drive motor, a rotating mechanism and a pneumatic gripper. The pneumatic gripper There are two, namely the loading gripper and the unloading gripper; the two CNC machine tools 2 are respectively located at the lower left and lower rig...
PUM
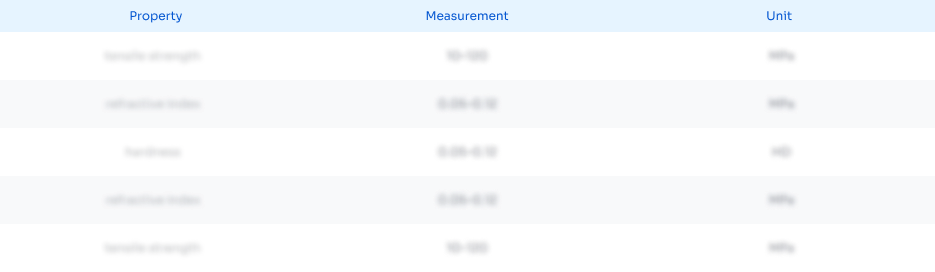
Abstract
Description
Claims
Application Information

- R&D
- Intellectual Property
- Life Sciences
- Materials
- Tech Scout
- Unparalleled Data Quality
- Higher Quality Content
- 60% Fewer Hallucinations
Browse by: Latest US Patents, China's latest patents, Technical Efficacy Thesaurus, Application Domain, Technology Topic, Popular Technical Reports.
© 2025 PatSnap. All rights reserved.Legal|Privacy policy|Modern Slavery Act Transparency Statement|Sitemap|About US| Contact US: help@patsnap.com