Ball type hot blast stove burning process control method and system
A process control and hot blast stove technology, applied in steel manufacturing process, furnaces, blast furnaces, etc., can solve the problems of real-time precise control of the burning process of difficult-to-hot blast stoves, and achieve the effect of real-time precise control
- Summary
- Abstract
- Description
- Claims
- Application Information
AI Technical Summary
Problems solved by technology
Method used
Image
Examples
Embodiment 1
[0069] refer to figure 1 , The method for controlling the firing process of a spherical hot blast stove provided in Embodiment 1 of the present invention includes:
[0070] Step S101, based on the historical data of the hot blast stove, matching to obtain the best air-fuel ratio;
[0071] Step S102, according to the gas-solid two-phase heat transfer in the furnace and the process structure, establish a transient heat transfer model of the regenerator of the hot blast stove;
[0072] Step S103, based on the transient heat transfer model of the regenerator of the hot blast stove, a temperature prediction model is established, and the temperature prediction model includes a vault temperature prediction model and an exhaust gas temperature prediction model;
[0073] In step S104, based on the temperature prediction model, the optimal control parameters for controlling the firing process of the hot blast stove are obtained in real time.
[0074] The method for controlling the fir...
Embodiment 2
[0077] refer to figure 2 , the method for controlling the firing process of a spherical hot blast stove provided in Embodiment 2 of the present invention includes:
[0078] Step S201, preprocessing the collected historical data of hot blast stove firing.
[0079] Due to the existence of interference, the data collected in this embodiment is incomplete or inaccurate, so the Lagrangian interpolation method is used to process the missing values; to preserve the shape and width of the data, Savitzky-Golay filtering is used; to eliminate The impact of the variable dimension on the calculation is normalized for each variable.
[0080] Step S202, re-describing the state parameter vector and the operation parameter vector through a limited time window, so as to obtain an operation mode conforming to the process.
[0081] Data in complex industrial production processes mainly include operating parameters and state parameters. The operating parameters at time τ can be expressed as: ...
PUM
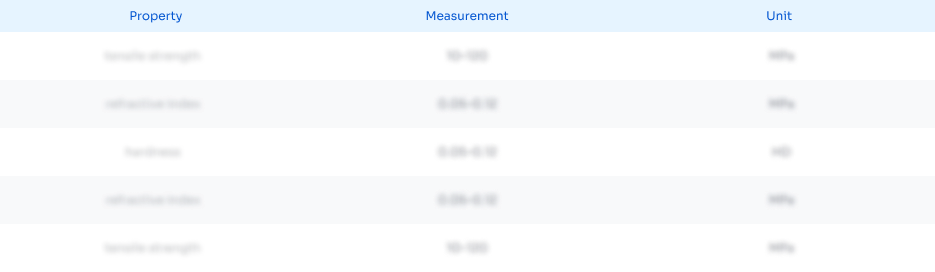
Abstract
Description
Claims
Application Information

- Generate Ideas
- Intellectual Property
- Life Sciences
- Materials
- Tech Scout
- Unparalleled Data Quality
- Higher Quality Content
- 60% Fewer Hallucinations
Browse by: Latest US Patents, China's latest patents, Technical Efficacy Thesaurus, Application Domain, Technology Topic, Popular Technical Reports.
© 2025 PatSnap. All rights reserved.Legal|Privacy policy|Modern Slavery Act Transparency Statement|Sitemap|About US| Contact US: help@patsnap.com