Heating processing device and processing technology for manufacturing pressure dies
A pressure mold and heat treatment technology, applied in the field of pressure molds, can solve the problems of inability to guarantee the quality of installation, damage to assembly parts, and high control costs, achieve smooth and continuous changes in lateral temperature distribution, reduce manufacturing costs, and improve production efficiency and quality effect
- Summary
- Abstract
- Description
- Claims
- Application Information
AI Technical Summary
Problems solved by technology
Method used
Image
Examples
Embodiment Construction
[0029] In order to make the purpose, technical features and technical effects of the technical solution of the present invention more clear, the exemplary solutions of the embodiments of the present invention will be clearly and completely described below in conjunction with the drawings of specific embodiments of the present invention.
[0030] Each embodiment in this specification is described in a progressive manner, each embodiment focuses on the difference from other embodiments, and the same or similar parts of each embodiment can be referred to each other.
[0031] Aiming at many problems existing in the wire drawing die manufacturing process, the embodiment of the present invention, see figure 1 As shown, a heat treatment device for pressure mold manufacturing is provided, including: a workbench; an electromagnetic induction heater arranged on the workbench; and a station for placing a pressure mold to be heated on the workbench; The heat treatment of the pressure mold...
PUM
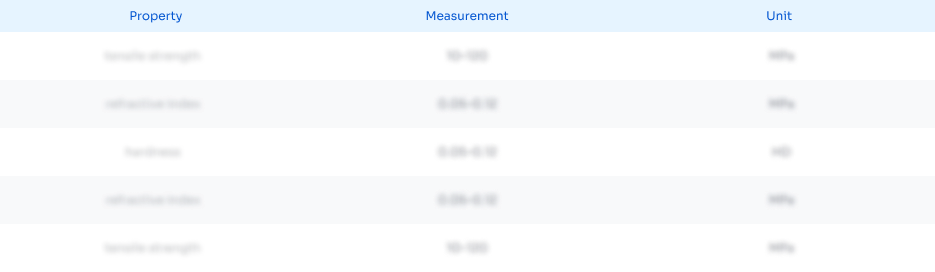
Abstract
Description
Claims
Application Information

- Generate Ideas
- Intellectual Property
- Life Sciences
- Materials
- Tech Scout
- Unparalleled Data Quality
- Higher Quality Content
- 60% Fewer Hallucinations
Browse by: Latest US Patents, China's latest patents, Technical Efficacy Thesaurus, Application Domain, Technology Topic, Popular Technical Reports.
© 2025 PatSnap. All rights reserved.Legal|Privacy policy|Modern Slavery Act Transparency Statement|Sitemap|About US| Contact US: help@patsnap.com