Switch laser cutting machine and cutting machining method
A laser cutting machine, laser head technology, applied in laser welding equipment, metal processing equipment, manufacturing tools and other directions, can solve the problems of reducing machine tool durability, machine tool wear, reducing cutting efficiency, etc., to reduce downtime waiting time, The effect of improving operation stability and improving cutting efficiency
- Summary
- Abstract
- Description
- Claims
- Application Information
AI Technical Summary
Problems solved by technology
Method used
Image
Examples
Embodiment Construction
[0032] The structural principle and working principle of the present invention will be further described in detail below in conjunction with the accompanying drawings.
[0033] like Figure 1 ~ Figure 4 As shown, an exchange laser cutting machine includes a machine tool 1, a feeding table 2, a laser head 3, an X-axis drive mechanism 4, a Y-axis drive mechanism 5, a Z-axis drive mechanism 6, a workbench 7, and a drive workbench 7 up and down The moving elevating mechanism 8 and the driving mechanism 9 that drives the workbench 7 to move back and forth between the machine tool 1 and the loading platform 2, the loading platform 2 is arranged at the front end of the machine tool 1, and the X-axis driving mechanism 4 is arranged at On the machine tool 1, the Y-axis driving mechanism 5 is arranged on the X-axis driving mechanism 4, the Y-axis driving mechanism 5 can move back and forth on the X-axis driving mechanism 4, and the Z-axis driving mechanism 6 is arranged on the Y-axis dr...
PUM
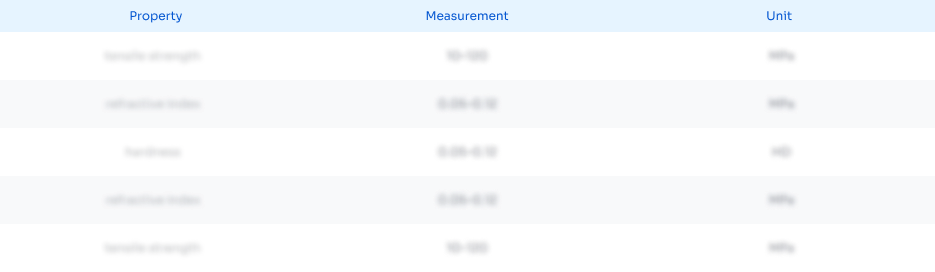
Abstract
Description
Claims
Application Information

- R&D
- Intellectual Property
- Life Sciences
- Materials
- Tech Scout
- Unparalleled Data Quality
- Higher Quality Content
- 60% Fewer Hallucinations
Browse by: Latest US Patents, China's latest patents, Technical Efficacy Thesaurus, Application Domain, Technology Topic, Popular Technical Reports.
© 2025 PatSnap. All rights reserved.Legal|Privacy policy|Modern Slavery Act Transparency Statement|Sitemap|About US| Contact US: help@patsnap.com