Method for machining of ball tracks of inner races of constant velocity joints
A ball track and constant velocity joint technology, applied in the field of quick joints, can solve problems such as low efficiency, increase complexity and cost, and achieve the effect of reducing complexity and time requirements
- Summary
- Abstract
- Description
- Claims
- Application Information
AI Technical Summary
Problems solved by technology
Method used
Image
Examples
Embodiment Construction
[0066] A power scraping tool 1 according to an exemplary embodiment is shown in a perspective view together with an exemplary workpiece 2 . The tool 1 comprises a tool body 10 which may be described as a ring or disk extending along an axial direction A which is aligned with an axis of rotation R of the tool and along a radial direction R t1 coincide. A plurality of cutting members in the form of replaceable inserts 100 are equally spaced along the perimeter P of the tool body.
[0067] The shown tool body 10 is a steel body and is suitable for attaching the tool by engagement by means of a central hole H to a spindle providing rotational movement to the tool.
[0068] The outer diameter of the tool body of the illustrated embodiment, ie the diameter at the periphery of the tool body, is about 150 mm. also, figure 1 The illustrated exemplary embodiment includes twelve cutting inserts 100 arranged along the periphery of the cutter body, the design of which will be described ...
PUM
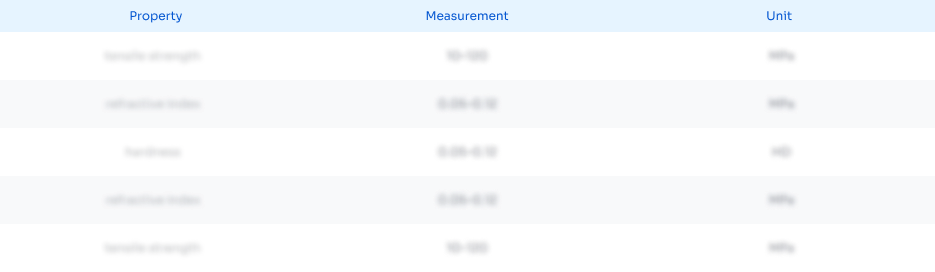
Abstract
Description
Claims
Application Information

- R&D Engineer
- R&D Manager
- IP Professional
- Industry Leading Data Capabilities
- Powerful AI technology
- Patent DNA Extraction
Browse by: Latest US Patents, China's latest patents, Technical Efficacy Thesaurus, Application Domain, Technology Topic, Popular Technical Reports.
© 2024 PatSnap. All rights reserved.Legal|Privacy policy|Modern Slavery Act Transparency Statement|Sitemap|About US| Contact US: help@patsnap.com