Bridge bottom surface detection device and method
A detection device and bridge technology, applied in the field of machinery, can solve the problems of difficult and accurate splicing of photos, large amount of calculation, large computing resources, etc.
- Summary
- Abstract
- Description
- Claims
- Application Information
AI Technical Summary
Problems solved by technology
Method used
Image
Examples
Embodiment 1
[0032] Such as Figure 1-3 The shown bridge bottom detection device includes two support rails 1 fixed on the bridge, a working platform 2 is slidably connected between the two support rails 1, and at least three detection robots 7 are slidably installed on the working platform 2 It is a group of coordinated detection units; the detection robot 7 includes a walking movement part 3, and the walking movement part 3 is connected with the detection work part 5 through the extension arm 4; the detection work part 5 is equipped with a camera 6; the work platform 2 and the detection robot 7 There are remote data centers with wired or wireless connections. The extension arm 4 includes a base 43 rotatably connected to the running part, the base 43 is articulated to a first articulated arm 41 , the first articulated arm 41 is articulated to a second articulated arm 42 , and the second articulated arm 42 is connected to the working platform 2 . Because there is no GPS signal easily at t...
Embodiment 2
[0038] A bridge bottom detection method, comprising the steps of:
[0039] Step 1. Carry out measurement and three-dimensional modeling of the bottom structure of the bridge body through the remote data center;
[0040]Step 2, according to the characteristics of each box mechanism at the bottom of the bridge body, it is divided into several measurement units; the measurement unit is the bridge area where the quality of the photos taken by the camera 6 reaches a specified level when the detection robot 7 is not adjusted; specifically The photos taken by the camera 6 within a certain focus range are clear, and within the range of the measurement unit, the distance between the camera and the corresponding shooting surface is within the focus range of the camera 6, thereby ensuring the degree of cleaning of the photos taken. Within the scope of the measurement unit, it is only necessary to make the working platform 2 run along the support rail. After each measurement unit is shot,...
Embodiment 3
[0044] Such as Figure 5 As shown, in order to realize the fixation of the robot on the working platform 2, the motor 10 is a self-locking motor; the roller 9 is a gear, and there are several teeth that cooperate with the gears along the length direction of the working platform 2; Surface snug setting.
PUM
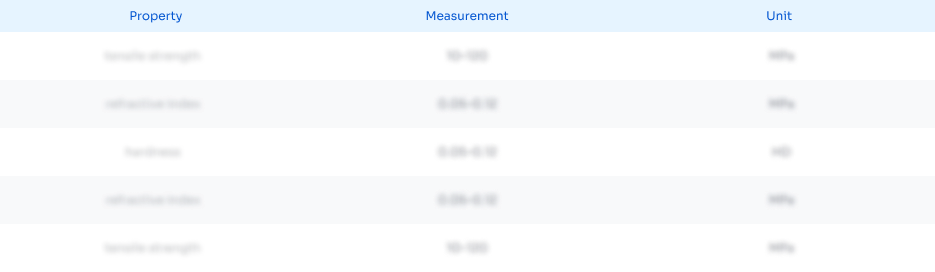
Abstract
Description
Claims
Application Information

- R&D
- Intellectual Property
- Life Sciences
- Materials
- Tech Scout
- Unparalleled Data Quality
- Higher Quality Content
- 60% Fewer Hallucinations
Browse by: Latest US Patents, China's latest patents, Technical Efficacy Thesaurus, Application Domain, Technology Topic, Popular Technical Reports.
© 2025 PatSnap. All rights reserved.Legal|Privacy policy|Modern Slavery Act Transparency Statement|Sitemap|About US| Contact US: help@patsnap.com