Production process for wool polar fleece
A production process, the technology of polar fleece, applied in the field of wool polar fleece production technology, can solve the problems of deterioration, graining difficulty, and the decline of wool use value, etc., and achieve the effect of good warmth retention, breathability and comfort
- Summary
- Abstract
- Description
- Claims
- Application Information
AI Technical Summary
Problems solved by technology
Method used
Image
Examples
Embodiment Construction
[0016] A production process for wool polar fleece, comprising the steps of:
[0017] 1) weaving: select 50NM wool nitrile+75D+200D polar fleece to weave;
[0018] 2) Bleaching and dyeing: choose the required fuel to dye the finished blank. Wool uses Huntsman CE-01 yellow, CE red, CE blue; 3 RL-ED yellow, GRL-ED red, GSL-ED blue dyeing, dyeing temperature 105 ℃ 45MIN;
[0019] 3) water rolling and cutting: use water squeezing machine to carry out preliminary dewatering to the finished blank of bleaching and dyeing, then carry out opening process to cylinder light blank with cutting machine;
[0020] 4) Drying: Dry the blank at a speed of 20m / min at 110°C;
[0021] 5) Stenter setting: use a stenter setting machine to open the blank and set the temperature at 110°C / 45S;
[0022] 6) Surface treatment: brushing: use 24-roller straight looper combination, connect eight times, add combing / shearing, and the hair height is measured between 3.5-4.5mm.
[0023] Shake grains: continuo...
PUM
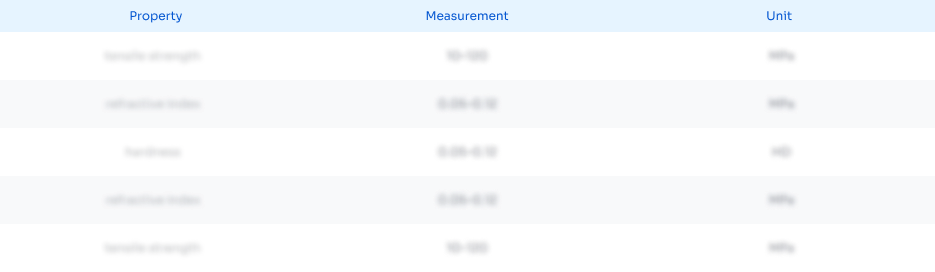
Abstract
Description
Claims
Application Information

- Generate Ideas
- Intellectual Property
- Life Sciences
- Materials
- Tech Scout
- Unparalleled Data Quality
- Higher Quality Content
- 60% Fewer Hallucinations
Browse by: Latest US Patents, China's latest patents, Technical Efficacy Thesaurus, Application Domain, Technology Topic, Popular Technical Reports.
© 2025 PatSnap. All rights reserved.Legal|Privacy policy|Modern Slavery Act Transparency Statement|Sitemap|About US| Contact US: help@patsnap.com