Microwave premelting and full melting process for glass batch materials and equipment thereof
A glass batching and batching technology, applied in electric furnaces, furnaces, retort furnaces, etc., can solve the problems of large investment, environmental pollution, low thermal efficiency, etc., to avoid environmental pollution, reduce greenhouse gases, and simple furnace structure. Effect
- Summary
- Abstract
- Description
- Claims
- Application Information
AI Technical Summary
Problems solved by technology
Method used
Image
Examples
Embodiment Construction
[0015] figure 1 In the process, the glass batch material is put into the vertical batch material bin 1, and microwave heating devices 5 are arranged around the outer side wall of the vertical batch bin 1, and they gradually heat the glass batch material from top to bottom to make it After completing dehydration drying, chemical thermal decomposition, solid-phase sintering and semi-molten state, it will automatically flow out from the bottom of the vertical matching silo 1 under the action of gravity, and then fall into the traditional glass kiln feeding pool 8 with flame as the heat source below it. In the process, the molten glass 6 passes through the melting and clarification tank 9 of the traditional glass tank kiln and the cooling forming tank 10 of the traditional glass tank kiln, and finally completes the melting, clarification, homogenization and cooling processes in the molten glass melting process, and is sent to the glass forming process. The process is to form glass...
PUM
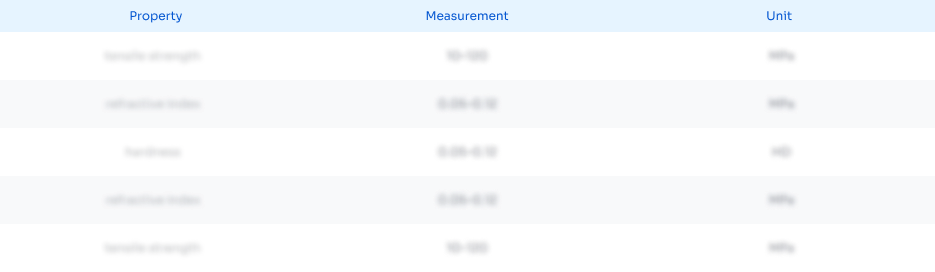
Abstract
Description
Claims
Application Information

- R&D
- Intellectual Property
- Life Sciences
- Materials
- Tech Scout
- Unparalleled Data Quality
- Higher Quality Content
- 60% Fewer Hallucinations
Browse by: Latest US Patents, China's latest patents, Technical Efficacy Thesaurus, Application Domain, Technology Topic, Popular Technical Reports.
© 2025 PatSnap. All rights reserved.Legal|Privacy policy|Modern Slavery Act Transparency Statement|Sitemap|About US| Contact US: help@patsnap.com