Production device and processing method for expansive glass hoses
A production device and expansive technology, applied in the field of fiber tubes, can solve problems such as uneven quality, uneven thickness of fiber hose impregnated paint, and increased production costs
- Summary
- Abstract
- Description
- Claims
- Application Information
AI Technical Summary
Problems solved by technology
Method used
Image
Examples
Embodiment 1
[0026] refer to Figure 1 to Figure 6 As shown, the present invention is an expandable glass hose production device, which includes a feeding roller group 1, several parallel paint dipping mechanisms 2 and winding mechanisms 3, and the feeding roller group 1 includes several horizontally spaced The rotating shaft of the paint dipping mechanism 2 includes a guide mechanism 4, a stretching mechanism 5, a paint dipping assembly 6 and a drying box 7, and the stretching mechanism 5, the paint dipping assembly 6 and the drying box 7 are from bottom to top The guide mechanism 4 includes a first guide assembly arranged directly under the expansion mechanism 5 and a second guide assembly arranged on the top of the drying box 7, and the winding mechanism 3 includes a set of directional rollers 8 and several rewinding assemblies arranged at intervals, the expansion mechanism 5 includes a cone 51 and a limit ring 52 for the fiber hose to pass through, the cone 51 is placed in the center o...
Embodiment 2
[0035] A processing method for an expandable glass hose production device, comprising the following steps:
[0036] 1) Put the fiber hoses wound on the rollers to be impregnated on the rotating rollers of the feeding roller group 1 respectively; put the mason cone 51 into the fiber hoses;
[0037] 2) Pass the end of the fiber hose around the guide roller 41, pass through the stop ring 52, the paint scraping plate 64 and the drying box 7 from bottom to top, and bypass the rotating roller of the steering shaft 45 and the orientation roller group 8 , and finally wound on the winding roller 31;
[0038] 3) Put the containing barrel 62 full of glue paint upside down in the glue paint box 61, when the liquid level in the glue paint box 61 is lower than the output end of the containing barrel 62, the glue paint in the containing barrel 62 flows out, and the fiber hose is supported After opening, through the glue paint box 61, the outside of the fiber hose is covered with glue paint,...
PUM
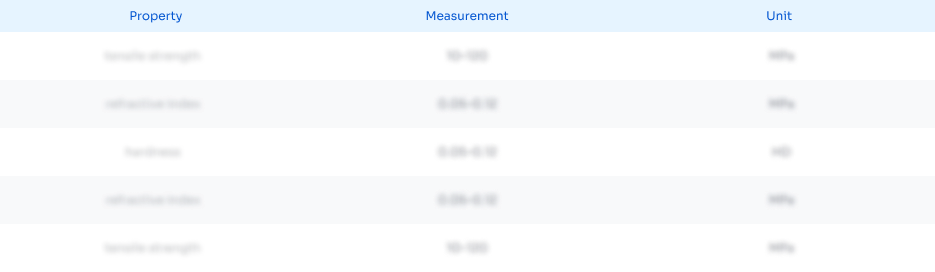
Abstract
Description
Claims
Application Information

- R&D
- Intellectual Property
- Life Sciences
- Materials
- Tech Scout
- Unparalleled Data Quality
- Higher Quality Content
- 60% Fewer Hallucinations
Browse by: Latest US Patents, China's latest patents, Technical Efficacy Thesaurus, Application Domain, Technology Topic, Popular Technical Reports.
© 2025 PatSnap. All rights reserved.Legal|Privacy policy|Modern Slavery Act Transparency Statement|Sitemap|About US| Contact US: help@patsnap.com