Self tin adhesion welding head used for junction box bus bar welding machine
A tin welding and bus bar technology, applied in the field of bus bar welding machines, can solve problems affecting production efficiency, poor product quality, uneven and smooth surface, etc.
- Summary
- Abstract
- Description
- Claims
- Application Information
AI Technical Summary
Problems solved by technology
Method used
Image
Examples
Embodiment Construction
[0016] The following will clearly and completely describe the technical solutions in the embodiments of the present invention with reference to the drawings in the embodiments of the present invention.
[0017] Such as Figure 1 to Figure 5 As shown, a self-adhesive solder joint 2 for a junction box bus bar welding machine is installed on the welding bracket 1 of the bus bar welding machine;
[0018] The self-adhesive soldering joint 2 is U-shaped as a whole and forms a vertical crack 22 in the middle. The bottom 23 of the crack 22 gradually widens and the bottom protrudes upwards in an arc shape. Such a soldering joint improves the heat exchange of the surrounding environment during the heat conduction process. Effect;
[0019] The bottom of the self-adhesive solder joint 2 is horizontally provided with a groove 25, and the side of the groove 25 is provided with an arched protrusion 251, and in cooperation with the groove 251, we will use the Luotie head in the Luotie proces...
PUM
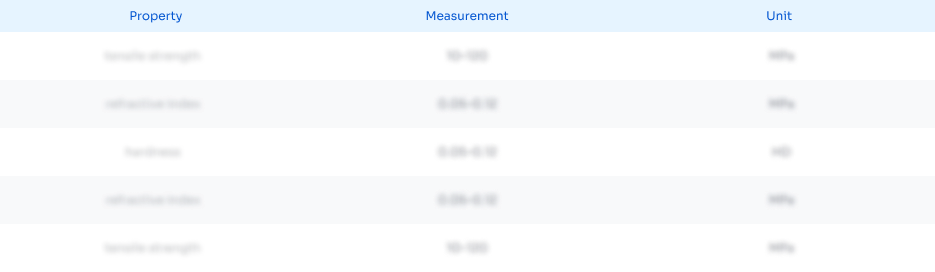
Abstract
Description
Claims
Application Information

- R&D Engineer
- R&D Manager
- IP Professional
- Industry Leading Data Capabilities
- Powerful AI technology
- Patent DNA Extraction
Browse by: Latest US Patents, China's latest patents, Technical Efficacy Thesaurus, Application Domain, Technology Topic, Popular Technical Reports.
© 2024 PatSnap. All rights reserved.Legal|Privacy policy|Modern Slavery Act Transparency Statement|Sitemap|About US| Contact US: help@patsnap.com