Novel high speed pantograph and lightweight dynamic design method thereof
A pantograph and lightweight technology, applied in the field of new high-speed pantograph and its lightweight dynamic design, can solve the problems of aggravating the end wear of the carbon skateboard and increasing the high-frequency vibration mass, and reduce the wear of the wheel and rail. Effects of contact dynamics
- Summary
- Abstract
- Description
- Claims
- Application Information
AI Technical Summary
Problems solved by technology
Method used
Image
Examples
Embodiment Construction
[0053] In order to make the objectives, technical solutions, and advantages of the embodiments of the present invention clearer, the technical solutions in the embodiments of the present invention will be described clearly and completely in conjunction with the accompanying drawings in the embodiments of the present invention. Obviously, the described embodiments It is a part of the embodiments of the present invention, not all the embodiments. Based on the embodiments of the present invention, all other embodiments obtained by those of ordinary skill in the art without creative work shall fall within the protection scope of the present invention.
[0054] Such as figure 1 As shown, the embodiment of the present invention provides a new high-speed pantograph lightweight dynamic design method and software analysis flow block diagram. The high-speed described in this embodiment refers to the operating speed of 400km / h and above, which specifically includes the following 5 The main...
PUM
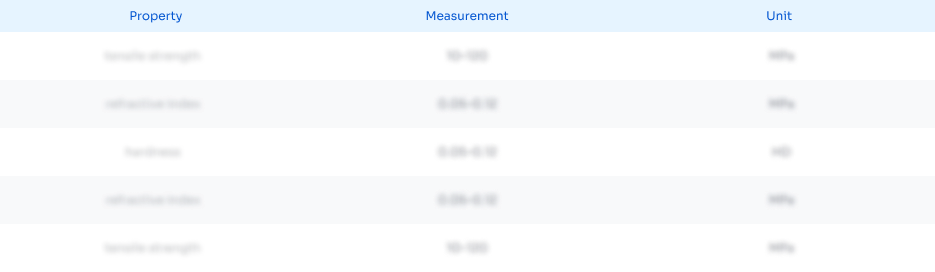
Abstract
Description
Claims
Application Information

- R&D
- Intellectual Property
- Life Sciences
- Materials
- Tech Scout
- Unparalleled Data Quality
- Higher Quality Content
- 60% Fewer Hallucinations
Browse by: Latest US Patents, China's latest patents, Technical Efficacy Thesaurus, Application Domain, Technology Topic, Popular Technical Reports.
© 2025 PatSnap. All rights reserved.Legal|Privacy policy|Modern Slavery Act Transparency Statement|Sitemap|About US| Contact US: help@patsnap.com