Production process for aluminum alloy battery boxes
A production process and battery box technology, which is applied in the production process field of aluminum alloy battery boxes, can solve problems such as easy damage, battery stability, and insufficient safety, and achieve the effects of simple process, avoiding box cracking, and high strength
- Summary
- Abstract
- Description
- Claims
- Application Information
AI Technical Summary
Problems solved by technology
Method used
Examples
Embodiment 1
[0019] The present invention proposes a kind of production technology of aluminum alloy battery case, comprises the following steps:
[0020] S1: Raw material preparation, the raw materials are as follows by weight: 0.7 parts of tungsten block, 0.7 part of iron block, 0.4 part of titanium block, 0.4 part of zinc block, 0.1 part of zirconium block, 0.2 part of magnesium block, 1 part of nickel block, 3 parts of manganese block 70 parts and aluminum block;
[0021] S2: Weigh the aluminum block in proportion, put the aluminum block in the melting furnace, and melt the aluminum block at 650 degrees Celsius. After it is completely melted, filter it to remove impurities in the solution And the particles in it can form aluminum solution and will be kept warm for later use
[0022] S3: Put the tungsten block, iron block, titanium block, zinc block, zirconium block, magnesium block, nickel block and manganese block obtained in S1 into the melting furnace in descending order according ...
Embodiment 2
[0032] The present invention proposes a kind of production technology of aluminum alloy battery case, comprises the following steps:
[0033] S1: Raw material preparation, the raw materials are as follows by weight: 0.9 parts of tungsten block, 0.9 part of iron block, 0.6 part of titanium block, 0.6 part of zinc block, 0.3 part of zirconium block, 0.3 part of magnesium block, 2 parts of nickel block, 4 parts of manganese block 74 parts and aluminum block;
[0034] S2: Weigh the aluminum block in proportion, put the aluminum block in the smelting furnace, and melt the aluminum block at 650-690 degrees Celsius, and filter it after it is completely melted, so that the solution can be removed The impurities and the particles in it can form aluminum solution, which will be kept warm for later use
[0035] S3: Put the tungsten block, iron block, titanium block, zinc block, zirconium block, magnesium block, nickel block and manganese block obtained in S1 into the smelting furnace in...
Embodiment 3
[0045] The present invention proposes a kind of production technology of aluminum alloy battery case, comprises the following steps:
[0046] S1: Raw material preparation, the raw materials are as follows by weight: 1.1 parts of tungsten block, 1.1 part of iron block, 0.7 part of titanium block, 0.7 part of zinc block, 0.4 part of zirconium block, 0.5 part of magnesium block, 2 parts of nickel block, 4 parts of manganese block 76 parts and aluminum block;
[0047] S2: Weigh the aluminum block in proportion, put the aluminum block in the melting furnace, and melt the aluminum block at 680 degrees Celsius. After it is completely melted, filter it to remove impurities in the solution And the particles in it can form aluminum solution and will be kept warm for later use
[0048] S3: Put the tungsten block, iron block, titanium block, zinc block, zirconium block, magnesium block, nickel block and manganese block obtained in S1 into the smelting furnace in descending order accordin...
PUM
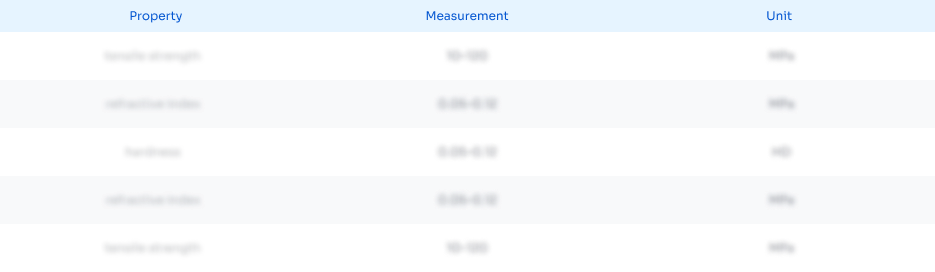
Abstract
Description
Claims
Application Information

- Generate Ideas
- Intellectual Property
- Life Sciences
- Materials
- Tech Scout
- Unparalleled Data Quality
- Higher Quality Content
- 60% Fewer Hallucinations
Browse by: Latest US Patents, China's latest patents, Technical Efficacy Thesaurus, Application Domain, Technology Topic, Popular Technical Reports.
© 2025 PatSnap. All rights reserved.Legal|Privacy policy|Modern Slavery Act Transparency Statement|Sitemap|About US| Contact US: help@patsnap.com