Preparation method of light modulation film based on liquid crystal/polymer composite material
A technology of liquid crystal materials and composite materials, applied in the field of preparation of dimming films based on liquid crystal/polymer composite materials, can solve the problems of reducing the brightness and contrast of display devices, reduce the anchoring effect, increase the size, and improve the comprehensive The effect of electro-optical properties
- Summary
- Abstract
- Description
- Claims
- Application Information
AI Technical Summary
Problems solved by technology
Method used
Image
Examples
Embodiment 1
[0030] The photopolymerizable monomers selected were lauryl methacrylate, trimethylolpropane triacrylate and pentaerythritol tetrakis(3-mercaptopropionate). Mix the polymerizable monomer with the nematic liquid crystal SLC1717 at a mass ratio of 35.0:65.0. The mass ratio between lauryl methacrylate, trimethylolpropane triacrylate and pentaerythritol tetrakis(3-mercaptopropionate) is 18.0:9.0:8.0. The mass of the photoinitiator benzoin dimethyl ether (651) is 3.0% of the total mass of the photopolymerizable monomers. After stirring evenly, the mixture is in a clear state at room temperature, and the mixture is poured into a liquid crystal cell with a cell thickness of 20 μm by the siphon principle, and then heated at room temperature with a light intensity of 10 mw / cm 2 , a wavelength of 365nm ultraviolet light irradiation for 5 minutes to form the polymer dispersed liquid crystal film of Example 1.
[0031] Measure the electro-optical performance curve (such as figure 2 sh...
Embodiment 2
[0034]The photopolymerizable monomers selected were lauryl methacrylate, trimethylolpropane triacrylate and pentaerythritol tetrakis(3-mercaptopropionate). Mix the polymerizable monomer with the nematic liquid crystal SLC1717 at a mass ratio of 35.0:65.0. The mass ratio between lauryl methacrylate, trimethylolpropane triacrylate and pentaerythritol tetrakis(3-mercaptopropionate) is 21.0:12.0:2.0. The mass of the photoinitiator benzoin dimethyl ether (651) is 3.0% of the total mass of the photopolymerizable monomers. After stirring evenly, the mixture is in a clear state at room temperature, and the mixture is poured into a liquid crystal cell with a cell thickness of 20 μm by the principle of siphon, and then heated at room temperature with a light intensity of 10 mw / cm 2 , a wavelength of 365nm ultraviolet light irradiation for 5 minutes to form the polymer dispersed liquid crystal film of Example 2.
[0035] Measure the electro-optical performance curve (such as Figure 4...
Embodiment 3
[0038] The photopolymerizable monomers selected were lauryl methacrylate, trimethylolpropane triacrylate and pentaerythritol tetrakis(3-mercaptopropionate). Mix the polymerizable monomer with the nematic liquid crystal SLC1717 at a mass ratio of 45.0:55.0. The mass ratio between lauryl methacrylate, trimethylolpropane triacrylate and pentaerythritol tetrakis(3-mercaptopropionate) is 18.0:9.0:8.0. The mass of the photoinitiator benzoin dimethyl ether (651) is 3.0% of the total mass of the photopolymerizable monomers. After stirring evenly, the mixture is in a clear state at room temperature, and the mixture is poured into a liquid crystal cell with a cell thickness of 20 μm by the principle of siphon, and then heated at room temperature with a light intensity of 10 mw / cm 2 , a wavelength of 365nm ultraviolet light irradiation for 5 minutes to form the polymer dispersed liquid crystal film of Example 3.
[0039] Measure the electro-optical performance curve (such as Figure 6...
PUM
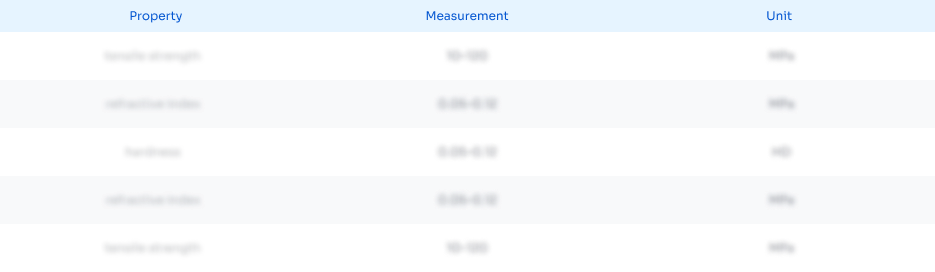
Abstract
Description
Claims
Application Information

- R&D
- Intellectual Property
- Life Sciences
- Materials
- Tech Scout
- Unparalleled Data Quality
- Higher Quality Content
- 60% Fewer Hallucinations
Browse by: Latest US Patents, China's latest patents, Technical Efficacy Thesaurus, Application Domain, Technology Topic, Popular Technical Reports.
© 2025 PatSnap. All rights reserved.Legal|Privacy policy|Modern Slavery Act Transparency Statement|Sitemap|About US| Contact US: help@patsnap.com