Plate mesh cage and plate mesh cage welding and positioning and transferring devices
A transfer device, welding positioning technology, applied in the direction of auxiliary equipment, welding equipment, auxiliary welding equipment, etc., can solve the problems of affecting production, labor-intensive, different sizes, etc.
- Summary
- Abstract
- Description
- Claims
- Application Information
AI Technical Summary
Problems solved by technology
Method used
Image
Examples
Embodiment Construction
[0035] The present invention will be further described in detail below in conjunction with the accompanying drawings, so that those skilled in the art can understand more clearly.
[0036] As plate net cage of the present invention, as figure 1 , figure 2 , image 3 shown, including:
[0037] The cage body 1, the upper part of the cage body is connected to several upper connecting pieces 2 along the length direction, and the upper connecting piece is provided with a circular through hole, and the lower part of the cage body is connected to several lower connecting pieces 3 along the length direction, The lower connecting piece is provided with waist-shaped through holes, and the waist-shaped through holes communicate with the circular through holes one by one.
[0038] The length of the waist-shaped through hole is not less than the diameter of the circular through hole, and the width of the waist-shaped through hole is smaller than the diameter of the circular through hol...
PUM
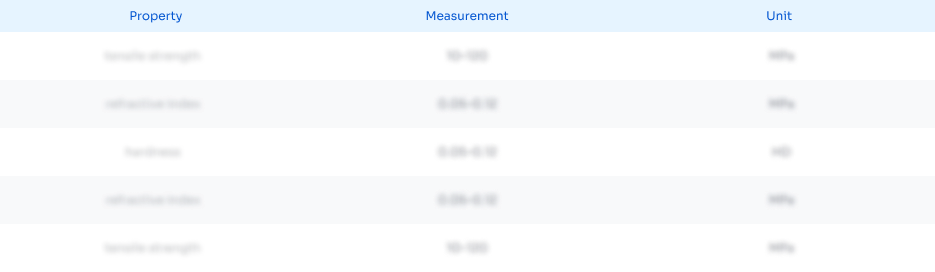
Abstract
Description
Claims
Application Information

- Generate Ideas
- Intellectual Property
- Life Sciences
- Materials
- Tech Scout
- Unparalleled Data Quality
- Higher Quality Content
- 60% Fewer Hallucinations
Browse by: Latest US Patents, China's latest patents, Technical Efficacy Thesaurus, Application Domain, Technology Topic, Popular Technical Reports.
© 2025 PatSnap. All rights reserved.Legal|Privacy policy|Modern Slavery Act Transparency Statement|Sitemap|About US| Contact US: help@patsnap.com