Machining process of gear
A processing technology and gear technology, which is applied in the field of gear processing technology, can solve the problems of transmission system safety hazards, low gear processing accuracy, and insufficient structural strength, etc., and achieve the effects of high structural strength, low cost, and improved casting accuracy
- Summary
- Abstract
- Description
- Claims
- Application Information
AI Technical Summary
Problems solved by technology
Method used
Examples
Embodiment 1
[0019] The present invention proposes a gear processing technology, which includes the following steps: S10: coating a layer of release agent on the inner cavity of the gear die-casting mold; S20: preheating the inner gear die-casting mold, the heating temperature is 400 ° C, and the heat preservation is 0.5 h; S30: heat the molten steel from the steel ingot to a molten state, and keep it warm at a temperature of 1300°C for 40 minutes; S40: continue heating the die-casting mold in step S10 so that its temperature reaches 1200°C, and Keep warm for 30 minutes, and pour the molten steel in S30 into the die-casting mold; S50: pressurize the die-casting mold at constant temperature from the pouring port immediately after the pouring is completed, and the pressure is 0.01MPa, and the pressurization time is kept for 40 minutes; S60 : cooling the die-casting mold to room temperature, and demoulding the gear; S70: grinding and polishing the gear in step S60 to form a finished gear.
Embodiment 2
[0021] The invention proposes a gear processing technology, which includes the following steps: S10: coating a layer of release agent on the inner cavity of the gear die-casting mold; S20: preheating the inner gear die-casting mold, the heating temperature is 600 ° C, and the heat preservation temperature is 0.8 h; S30: heat the molten steel from the steel ingot raw material to a molten state, and keep it warm at a temperature of 1500°C for 60 minutes; S40: continue heating the die-casting mold in step S10 so that its temperature reaches 1400°C, and Keep warm for 50 minutes, and pour the molten steel in S30 into the die-casting mold; S50: pressurize the die-casting mold at constant temperature from the pouring port immediately after the pouring is completed, and the pressure is 0.015MPa, and the pressurization time is maintained for 50 minutes; S60 : cooling the die-casting mold to room temperature, and demoulding the gear; S70: grinding and polishing the gear in step S60 to fo...
Embodiment 3
[0023] The invention proposes a gear processing technology, which includes the following steps: S10: coating a layer of release agent on the inner cavity of the gear die-casting mold; S20: preheating the inner gear die-casting mold, the heating temperature is 500 ° C, and the heat preservation is 0.7 h; S30: heat the molten steel ingot raw material to a molten state, and keep it warm, the keep temperature is 1400°C, and keep hold time is 50min; S40: continue to heat the die-casting mold in step S10 to make the temperature reach 1300°C, and Keep warm for 40 minutes, and pour the molten steel in S30 into the die-casting mold; S50: pressurize the die-casting mold at constant temperature from the pouring port immediately after the pouring is completed, and the pressure is 0.013MPa, and the pressurization time is kept for 45min; S60 : cooling the die-casting mold to room temperature, and demoulding the gear; S70: grinding and polishing the gear in step S60 to form a finished gear. ...
PUM
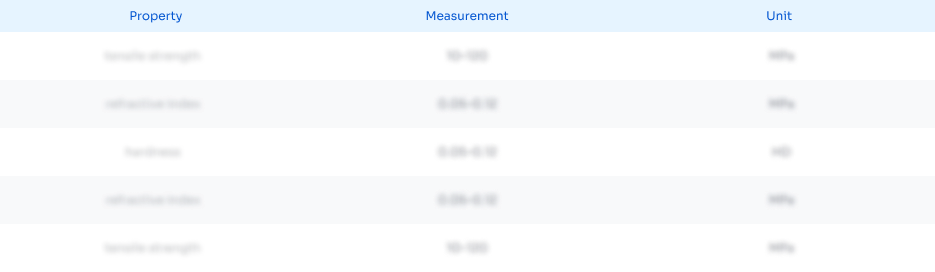
Abstract
Description
Claims
Application Information

- Generate Ideas
- Intellectual Property
- Life Sciences
- Materials
- Tech Scout
- Unparalleled Data Quality
- Higher Quality Content
- 60% Fewer Hallucinations
Browse by: Latest US Patents, China's latest patents, Technical Efficacy Thesaurus, Application Domain, Technology Topic, Popular Technical Reports.
© 2025 PatSnap. All rights reserved.Legal|Privacy policy|Modern Slavery Act Transparency Statement|Sitemap|About US| Contact US: help@patsnap.com