Power transmission tower foot welding process
A welding process, iron tower technology, applied in the direction of welding equipment, manufacturing tools, workpiece edge, etc., can solve the problems of long interval time, low welding efficiency, stress concentration, etc., to prevent stress concentration, good welding quality, prevent heat cumulative effect
- Summary
- Abstract
- Description
- Claims
- Application Information
AI Technical Summary
Problems solved by technology
Method used
Image
Examples
Embodiment Construction
[0024] The following will clearly and completely describe the technical solutions in the embodiments of the present invention in conjunction with the embodiments of the present invention. Obviously, the described embodiments are only part of the embodiments of the present invention, not all of them. Based on the implementation manners in the present invention, all other implementation manners obtained by persons of ordinary skill in the art without making creative efforts belong to the scope of protection of the present invention.
[0025] Such as Figure 4~5 As shown, the tower foot of the present invention includes a base A, a first main rib B, two second main ribs C and four slave ribs D, wherein the first main rib B is vertically welded on the surface of the base A, and the other two A second main rib C is arranged perpendicular to the base A and the first main rib B and is welded with them. Two second main ribs C are respectively arranged on both sides of the first main r...
PUM
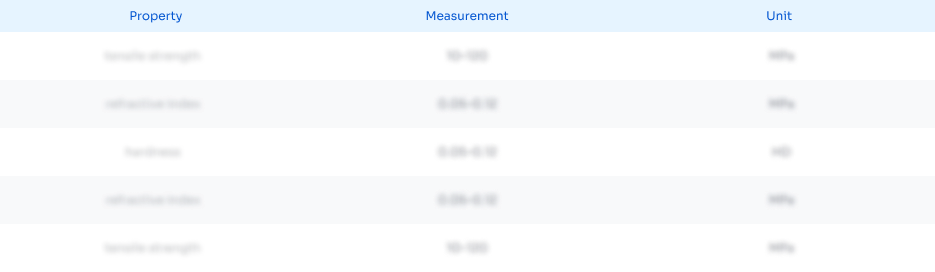
Abstract
Description
Claims
Application Information

- R&D Engineer
- R&D Manager
- IP Professional
- Industry Leading Data Capabilities
- Powerful AI technology
- Patent DNA Extraction
Browse by: Latest US Patents, China's latest patents, Technical Efficacy Thesaurus, Application Domain, Technology Topic, Popular Technical Reports.
© 2024 PatSnap. All rights reserved.Legal|Privacy policy|Modern Slavery Act Transparency Statement|Sitemap|About US| Contact US: help@patsnap.com