Two-stage sludge drying equipment system
A sludge drying, two-stage technology, applied in water/sludge/sewage treatment, dehydration/drying/thickened sludge treatment, multi-stage water treatment, etc., can solve complex operation, low calorific value, temperature rise Small and other problems, to achieve the effect of increasing the drying rate and reducing energy consumption
- Summary
- Abstract
- Description
- Claims
- Application Information
AI Technical Summary
Problems solved by technology
Method used
Image
Examples
Embodiment Construction
[0024] The present invention will be further described below in conjunction with the accompanying drawings.
[0025] refer to Figure 1 ~ Figure 4 , a two-stage sludge drying equipment system, including a heat source, a sludge packing module, a first-stage spiral drying module, a sludge extruding module, a second-stage tower cleaning and drying module, an exhaust gas purification module and a control box.
[0026] The packing device 10 is connected to the cylinder body 13; the outlet of the cylinder body 13 is connected to the extruding device 34; the extruding device 34 is connected to the tower body 37; Connected; the second level brush 27, the first level brush 35 and the third level brush 38 are installed on the hollow shaft 29; the tower body 37 is fixed with the second level grid plate 28, the first level grid plate 30, the third level grid plate 36 .
[0027] The control box can display and adjust the speed of the first section of the propeller blade and the second s...
PUM
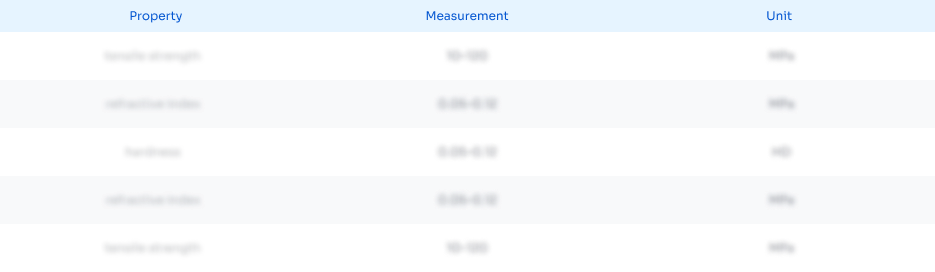
Abstract
Description
Claims
Application Information

- R&D Engineer
- R&D Manager
- IP Professional
- Industry Leading Data Capabilities
- Powerful AI technology
- Patent DNA Extraction
Browse by: Latest US Patents, China's latest patents, Technical Efficacy Thesaurus, Application Domain, Technology Topic, Popular Technical Reports.
© 2024 PatSnap. All rights reserved.Legal|Privacy policy|Modern Slavery Act Transparency Statement|Sitemap|About US| Contact US: help@patsnap.com