Production method of assembled bridge prefabricated member and industrial production line
A technology of prefabricated components and production methods, applied in the direction of manufacturing tools, unloading devices, mold auxiliary parts, etc., can solve the problems of high labor intensity for construction personnel, low prefabrication work efficiency, high prefabrication cost, etc., and achieve the effect of improving prefabrication work efficiency
- Summary
- Abstract
- Description
- Claims
- Application Information
AI Technical Summary
Problems solved by technology
Method used
Image
Examples
Embodiment 1
[0083] Example 1, such as figure 1 , as shown in 4-6:
[0084] A method for producing prefabricated bridge components, comprising the steps of:
[0085] Step 1, production line layout: Laying the pouring line on the construction site, the pouring line includes the first track 1, the side form assembly 2 matched with the side wall of the prefabricated component 5, and the movable set on the first track The trolley 3 on 1 is provided with a bottom mold 4 matching the shape of the bottom of the prefabricated component 5 on the trolley 3,
[0086] The first track 1 is divided into a reinforcement skeleton insertion area A and a mold casting area B along the length direction,
[0087] The side form assembly 2 is arranged on the construction site corresponding to the mold casting area B;
[0088] Step 2, hoisting the reinforcement skeleton: placing the reinforcement skeleton of the prefabricated component 5 on the bottom form 4;
[0089] Step 3, mold closing: after the reinforce...
Embodiment 2
[0113] Example 2, such as figure 2 , as shown in 4-6:
[0114] A production method for prefabricated bridge components 5. On the basis of Example 1, further, a curing area C is set after the mold-closing area B of the first track 1, and a maintenance area C is also set after the fifth step. There is step six, step six, prefabricated component 5 maintenance: in the step five, after the side form assembly 2 is separated from the concrete, the trolley 3 carries the prefabricated component 5 to the maintenance area C to perform the prefabricated component 5 maintenance process .
[0115] In the scheme of this embodiment, by setting the curing area C, after the prefabricated component 5 is separated from the side form assembly 2, the prefabricated component 5 will be transferred to the curing area C to perform the curing process. When the prefabricated component 5 needs to be stretched During construction, the prefabricated component 5 is first maintained to the initial tension ...
Embodiment 3
[0116] Example 3, such as image 3 , as shown in 4-6:
[0117] A production method of prefabricated bridge components 5, on the basis of Example 2, further, a tension traverse area D is also set after the maintenance area C of the first track 1, and after the sixth step Step 7, step 7, prefabricated component 5 stretching and traversing: in the step 6, after the maintenance of the prefabricated component 5 is completed, the trolley 3 carries the prefabricated component 5 to the stretching and traversing area D, firstly The prestressed tensioning construction of the prefabricated component 5, after the tensioning construction is completed, the prefabricated component 5 is hoisted to the storage position by the lifting device.
[0118] On the basis of the above embodiments, as a preferred manner, the arrangement of the production line in the first step further includes the layout of the loop line, and the arrangement of the loop line is: laying a loop line on the construction s...
PUM
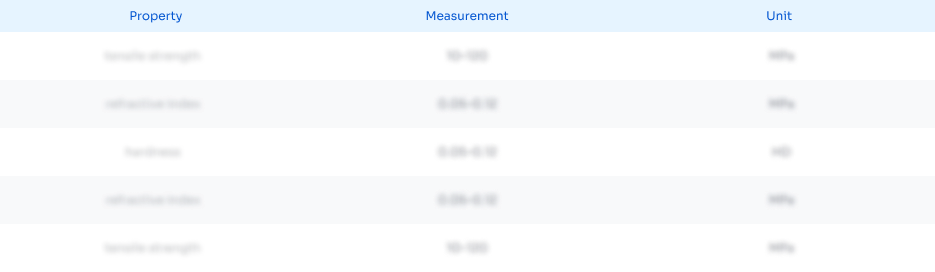
Abstract
Description
Claims
Application Information

- Generate Ideas
- Intellectual Property
- Life Sciences
- Materials
- Tech Scout
- Unparalleled Data Quality
- Higher Quality Content
- 60% Fewer Hallucinations
Browse by: Latest US Patents, China's latest patents, Technical Efficacy Thesaurus, Application Domain, Technology Topic, Popular Technical Reports.
© 2025 PatSnap. All rights reserved.Legal|Privacy policy|Modern Slavery Act Transparency Statement|Sitemap|About US| Contact US: help@patsnap.com