Method for preparing modified graphene/silica/styrene-butadiene rubber composite material
A technology of styrene-butadiene rubber and composite materials, which is applied in the field of preparation of graphene/white carbon black/styrene-butadiene rubber composite materials. Tear performance, effect of improving dispersion and uniformity
- Summary
- Abstract
- Description
- Claims
- Application Information
AI Technical Summary
Problems solved by technology
Method used
Examples
Embodiment 1
[0013] Add 1 part of graphene, 4 parts of kaolin, 30 parts of white carbon black, 100 parts by mass ratio of water, 0.1 g of sodium dodecylbenzenesulfonate as a dispersant, and stir at high speed for 30 minutes to prepare a uniformly dispersed slurry into the reactor. ; Take 100 parts of the mixed slurry and add it to the mixed emulsion mixed with 5 parts of natural rubber latex and 100 parts of styrene-butadiene latex (solid content 25%), mix under high-speed stirring, coagulate with acid, wash and dry to obtain modified graphite ene / silica / styrene-butadiene rubber composite material; get 100 parts of composite material, 50 parts of carbon black, 5 parts of zinc oxide, 3 parts of stearic acid, 2 parts of sulfur, 1 part of accelerator NS and mix on the open mill; Carry out vulcanization on the flat vulcanizer, vulcanization temperature 150 ℃. The physical and mechanical properties of the raw rubber are shown in Table 1.
Embodiment 2
[0015] Add 2 parts of graphene, 4 parts of kaolin, 30 parts of white carbon black, 100 parts by mass ratio of water, 0.1 g of sodium dodecylbenzenesulfonate as a dispersant, and stir at high speed for 30 minutes to prepare a uniformly dispersed slurry into the reactor. ; Take 100 parts of the mixed slurry and add it to the mixed emulsion mixed with 5 parts of natural rubber latex and 100 parts of styrene-butadiene latex (solid content 25%), mix under high-speed stirring, coagulate with acid, wash and dry to obtain modified graphite olefin / silica / styrene-butadiene rubber composite material; take 100 parts of composite material, 50 parts of carbon black, 5 parts of zinc oxide, 3 parts of stearic acid, 2 parts of sulfur, 1 part of accelerator NS, and knead on an open mill ; Vulcanize on a flat vulcanizer at a vulcanization temperature of 150°C. The physical and mechanical properties of the raw rubber are shown in Table 1.
Embodiment 3
[0017] Add 3 parts of graphene, 4 parts of kaolin, 30 parts of white carbon black, 100 parts by mass ratio of water, 0.1 g of sodium dodecylbenzenesulfonate as a dispersant, and stir at high speed for 30 minutes to prepare a uniformly dispersed slurry into the reactor. ; Take 100 parts of the mixed slurry and add it to the mixed emulsion mixed with 5 parts of natural rubber latex and 100 parts of styrene-butadiene latex (solid content 25%), mix under high-speed stirring, coagulate with acid, wash and dry to obtain modified graphite ene / silica / styrene-butadiene rubber composite material; get 100 parts of composite material, 50 parts of carbon black, 5 parts of zinc oxide, 3 parts of stearic acid, 2 parts of sulfur, 1 part of accelerator NS and mix on the open mill; Carry out vulcanization on the flat vulcanizer, vulcanization temperature 150 ℃. The physical and mechanical properties of the raw rubber are shown in Table 1.
PUM
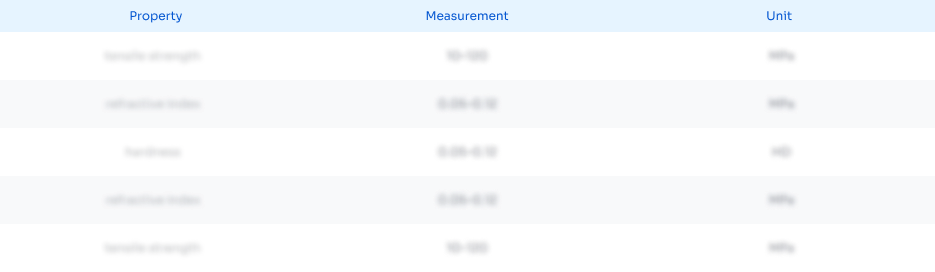
Abstract
Description
Claims
Application Information

- R&D Engineer
- R&D Manager
- IP Professional
- Industry Leading Data Capabilities
- Powerful AI technology
- Patent DNA Extraction
Browse by: Latest US Patents, China's latest patents, Technical Efficacy Thesaurus, Application Domain, Technology Topic, Popular Technical Reports.
© 2024 PatSnap. All rights reserved.Legal|Privacy policy|Modern Slavery Act Transparency Statement|Sitemap|About US| Contact US: help@patsnap.com