Flexible crawling robot with magnetic control variable friction and variable leg length functions
A crawling robot and variable friction technology, which is applied in the direction of program control manipulators, manipulators, manufacturing tools, etc., can solve the problems of low power density, non-adjustable leg length, slow response speed, etc., and achieve the effect of improving power density
- Summary
- Abstract
- Description
- Claims
- Application Information
AI Technical Summary
Problems solved by technology
Method used
Image
Examples
Embodiment Construction
[0029] The technical solutions of the present invention will be specifically described below in conjunction with the accompanying drawings and embodiments.
[0030] An embodiment of the present invention provides a soft crawling robot with magnetically controlled variable friction and variable leg length, including a friction variable mechanism and a leg length variable mechanism.
[0031] Such as Figures 1 to 6 As shown, the variable friction mechanism includes a bracket 1, a torsion spring 2, a magnet 3, an iron sheet 4, a variable friction sheet 5, and a rubber sheet 6. The bracket 1 includes an arcuate inner layer and an arcuate outer layer. A through hole is provided in the middle of the arcuate inner layer for fixing the cylindrical magnet 3. The middle of the arcuate outer layer passes through the slope structure and the step of the variable friction plate 5. The variable friction plate 5 is fixed, the outer surface of the variable friction plate 5 is pasted with a ru...
PUM
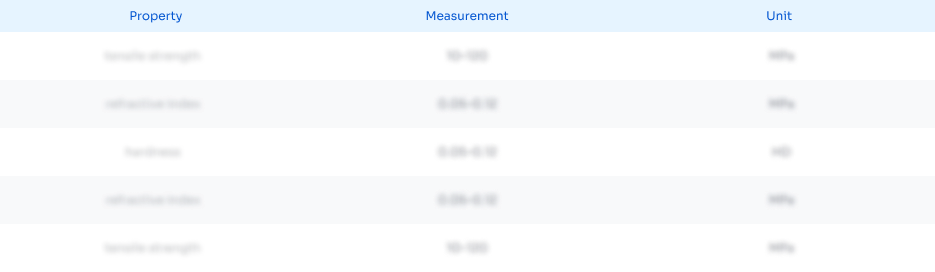
Abstract
Description
Claims
Application Information

- R&D Engineer
- R&D Manager
- IP Professional
- Industry Leading Data Capabilities
- Powerful AI technology
- Patent DNA Extraction
Browse by: Latest US Patents, China's latest patents, Technical Efficacy Thesaurus, Application Domain, Technology Topic, Popular Technical Reports.
© 2024 PatSnap. All rights reserved.Legal|Privacy policy|Modern Slavery Act Transparency Statement|Sitemap|About US| Contact US: help@patsnap.com