Preparation method of resin for photoresist
A technology of photoresist and resin, which is applied in the field of polymer resin preparation, can solve problems such as the introduction of impurities, limit the process of industrialization, and high toxicity, and achieve the effects of precise molecular weight control, simple implementation, and excellent application performance
- Summary
- Abstract
- Description
- Claims
- Application Information
AI Technical Summary
Problems solved by technology
Method used
Image
Examples
Embodiment 1
[0040] The preparation method of photoresist resin comprises the following steps:
[0041] (1) Take 35.62ml of tetrahydrofuran with water content of 200ppm into the reaction bottle, and heat it to 50-80°C for later use;
[0042] (2) Dissolve 9.87g of butyrolactone methacrylate, 7.05g of 3-hydroxy-2-adamantyl methacrylate, 15g of 1-ethylcyclohexyl methacrylate and 3.5g of azobisisobutyronitrile in In the THF of 74.83ml, obtain the THF solution of raw material;
[0043] (3) adding the tetrahydrofuran solution of the raw material obtained in step (2) dropwise into the preheated tetrahydrofuran containing moisture in step (1), and reacting at reflux at a constant temperature of 70 to 80°C for 15 hours;
[0044] (4) After the reaction is completed, cool to room temperature, precipitate the resin with n-hexane, filter and dry to obtain the resin for photoresist (1).
[0045] (5) The photoresist resin (1) can be obtained by GPC test, Mw=8900, PDI=1.62.
Embodiment 2
[0047] The preparation method of photoresist resin comprises the following steps:
[0048] (1) Take 35.62ml of tetrahydrofuran with water content of 400ppm into the reaction bottle, and heat it to 50-80°C for later use;
[0049] (2) Dissolve 9.87g of butyrolactone methacrylate, 7.05g of 3-hydroxy-2-adamantyl methacrylate, 15g of 1-ethylcyclohexyl methacrylate and 3.5g of azobisisobutyronitrile in In the THF of 74.83ml, obtain the THF solution of raw material;
[0050] (3) adding the tetrahydrofuran solution of the raw material obtained in step (2) dropwise into the preheated tetrahydrofuran containing moisture in step (1), and reacting under constant temperature reflux at 70-80°C for 15 hours;
[0051] (4) After the reaction is completed, cool to room temperature, precipitate the resin with n-hexane, filter and dry to obtain the resin for photoresist (2).
[0052] (5) The photoresist resin (2) can be obtained by GPC test, Mw=9200, PDI=1.57.
Embodiment 3
[0054] The preparation method of photoresist resin comprises the following steps:
[0055] (1) Take 35.62ml of tetrahydrofuran with water content of 500ppm into the reaction bottle, and heat it to 50-80°C for later use;
[0056] (2) Dissolve 9.87g of butyrolactone methacrylate, 7.05g of 3-hydroxy-2-adamantyl methacrylate, 15g of 1-ethylcyclohexyl methacrylate and 3.5g of azobisisobutyronitrile in In the THF of 74.83ml, obtain the THF solution of raw material;
[0057] (3) adding the tetrahydrofuran solution of the raw material obtained in the step (2) dropwise into the preheated tetrahydrofuran containing moisture in the step (1), and reacting at a constant temperature of 70 to 80° C. for 15 hours under reflux;
[0058] (4) After the reaction is completed, cool to room temperature, precipitate the resin with n-hexane, filter and dry to obtain the resin for photoresist (3).
[0059] (5) The photoresist resin (3) can be obtained by GPC test, Mw=9300, PDI=1.47.
PUM
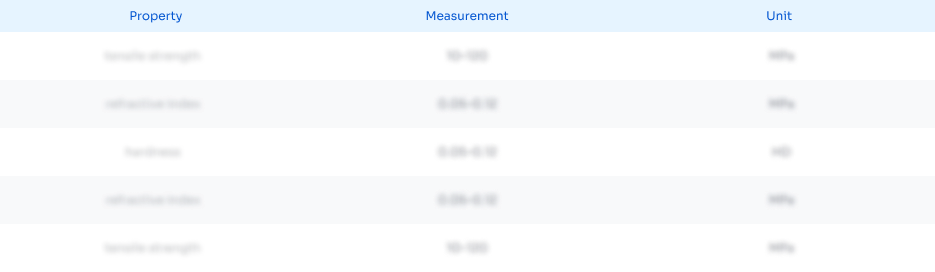
Abstract
Description
Claims
Application Information

- Generate Ideas
- Intellectual Property
- Life Sciences
- Materials
- Tech Scout
- Unparalleled Data Quality
- Higher Quality Content
- 60% Fewer Hallucinations
Browse by: Latest US Patents, China's latest patents, Technical Efficacy Thesaurus, Application Domain, Technology Topic, Popular Technical Reports.
© 2025 PatSnap. All rights reserved.Legal|Privacy policy|Modern Slavery Act Transparency Statement|Sitemap|About US| Contact US: help@patsnap.com