Crack-resistant rubber sole and production method thereof
A technology for rubber soles and rubber substrates, which can be used in shoe soles, footwear, applications, etc., can solve problems such as cracks and flex cracks, poor fit of midsoles, etc., and achieve the effect of simple preparation methods
- Summary
- Abstract
- Description
- Claims
- Application Information
AI Technical Summary
Problems solved by technology
Method used
Image
Examples
preparation example Construction
[0061] The present invention also provides a preparation method of the crack-resistant rubber sole described in the above technical solution, comprising the following steps:
[0062] a) Mix the rubber matrix, white carbon black, zinc oxide, lubricant, white smoke activator, p-phenylenediamine anti-aging agent, rubber protective wax, thiourea anti-aging agent, phenolic anti-aging agent and functional additives evenly, Carry out kneading, blanking obtains base material;
[0063] b) After kneading the base material obtained in step a), slice it and let it stand, then add insoluble sulfur and a rubber vulcanization accelerator and mix evenly, and finally release the sheet in sheet form to obtain a crack-resistant rubber sole.
[0064] In the present invention, the rubber matrix, white carbon black, zinc oxide, lubricant, white smoke activator, p-phenylenediamine anti-aging agent, rubber protective wax, thiourea anti-aging agent, phenolic anti-aging agent and functional auxiliary ...
Embodiment 1
[0076] The formula quantity of the raw materials used in Example 1 is shown in Table 1.
[0077] The formula quantity of raw material used in table 1 embodiment 1
[0078] raw material
parts by weight
Butadiene rubber
35
23.8
SBR
10
5
Silica
15
Zinc oxide
3
0.2
1.5
Anti-ozone protective wax
1
Di-n-octylthiourea
4
insoluble sulfur
1
N-tert-butyl-2-benzothiazole sulfenamide
0.5
[0079] (1) Butadiene rubber, natural rubber, styrene-butadiene rubber, white mineral oil, white carbon black, zinc oxide, stearic acid, diethylene glycol, anti-ozone protective wax and di-n-octyl thiourea in the above raw materials are The formula amounts in Table 1 were mixed evenly, mixed with an internal mixer at 120° C. for 20 minutes, and then cut to obtain the base material.
[0080] (2) After the ...
Embodiment 2
[0082] The formulation amount of the raw materials used in Example 2 is shown in Table 2.
[0083] The formula quantity of raw material used in table 2 embodiment 2
[0084] raw material
parts by weight
Butadiene rubber
45
natural rubber
10
Nitrile rubber
10
Silica
25
Zinc oxide
4
1.5
polyethylene glycol
2
1.2
Difurfurylthiourea
3.8
insoluble sulfur
0.7
dibenzothiazole disulfide
1
[0085] (1) Butadiene rubber, natural rubber, nitrile rubber, white carbon black, zinc oxide, plasticizer A, polyethylene glycol, microcrystalline wax and difurfuryl thiourea in the above-mentioned raw materials are according to the formula in table 2 Mix the formula amount evenly, knead at 120°C for 20 minutes with an internal mixer, and then cut to obtain the base material.
[0086] (2) After the base material obtained in step (1) is op...
PUM
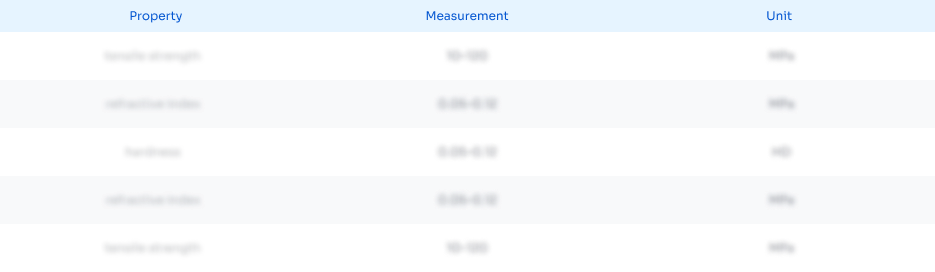
Abstract
Description
Claims
Application Information

- Generate Ideas
- Intellectual Property
- Life Sciences
- Materials
- Tech Scout
- Unparalleled Data Quality
- Higher Quality Content
- 60% Fewer Hallucinations
Browse by: Latest US Patents, China's latest patents, Technical Efficacy Thesaurus, Application Domain, Technology Topic, Popular Technical Reports.
© 2025 PatSnap. All rights reserved.Legal|Privacy policy|Modern Slavery Act Transparency Statement|Sitemap|About US| Contact US: help@patsnap.com