Triangular curved dovetail groove composite rudder substrate and installation method thereof
A technology of composite materials and dovetail grooves, applied in the direction of fuselage insulation, etc., can solve the problems of structural screw connections and increase the complexity of the assembly process, etc., to reduce the harsh thermal environment, ensure temperature requirements and reliability, and good heat insulation Effect
- Summary
- Abstract
- Description
- Claims
- Application Information
AI Technical Summary
Problems solved by technology
Method used
Image
Examples
Embodiment Construction
[0027] The present invention will be described in detail below in conjunction with the accompanying drawings and examples.
[0028] The invention improves the thermal environment around the rudder base plate by adopting the aerodynamic shape of the smooth triangular surface structure; it is installed on the surface of the aircraft through the trapezoidal dovetail groove of the rudder base plate and the dovetail block of the metal shell, simplifying the traditional heat-proof plug and multi-thread connection interface structure, The grinding process is reduced, and the operability of production assembly is improved; the composite material rudder substrate structure can play a role in heat protection for the rudder system of the aircraft actuator. Specifically, a hypersonic aircraft triangular curved dovetail groove composite material rudder substrate structure is generally located at the front end of the leading edge structure of the rudder system and installed on the outer surf...
PUM
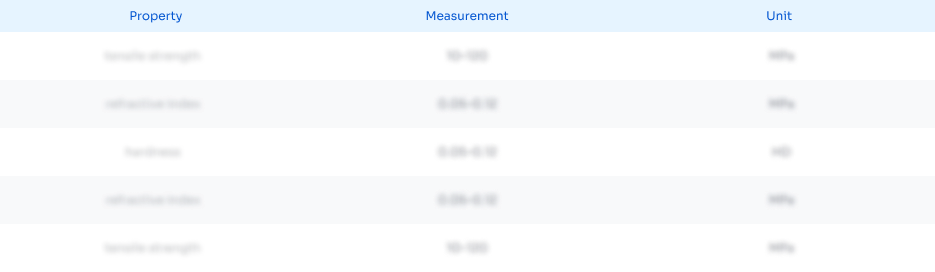
Abstract
Description
Claims
Application Information

- Generate Ideas
- Intellectual Property
- Life Sciences
- Materials
- Tech Scout
- Unparalleled Data Quality
- Higher Quality Content
- 60% Fewer Hallucinations
Browse by: Latest US Patents, China's latest patents, Technical Efficacy Thesaurus, Application Domain, Technology Topic, Popular Technical Reports.
© 2025 PatSnap. All rights reserved.Legal|Privacy policy|Modern Slavery Act Transparency Statement|Sitemap|About US| Contact US: help@patsnap.com