A kind of flame-retardant fiberglass composite material and its production process
A composite material and FRP technology, applied in the direction of synthetic resin layered products, layered products, chemical instruments and methods, etc., can solve the problems of looseness between fibers, inability to withstand bending, shearing and compressive stress, and difficult geometric shapes, etc. Achieve the effect of strong adsorption binding, good compatibility between layers, and stable spatial configuration
- Summary
- Abstract
- Description
- Claims
- Application Information
AI Technical Summary
Problems solved by technology
Method used
Image
Examples
Embodiment 1
[0025] The outer surface layer and the inner lining layer include the following components by weight: 30 parts of palygorskite / glass fiber composite fiber or its fabric containing zirconium phosphate, 12 parts of compound resin base, 0.8 part of flame retardant, and 2 parts of auxiliary additives;
[0026] The structural layer includes the following components by weight: 30 parts of palygorskite / glass fiber composite fiber or its fabric containing zirconium phosphate, 6 parts of compound resin base, 0.4 part of borax, and 3 parts of auxiliary additives;
[0027] The MCM / waste FRP composite resin material includes the following components by weight: 30 parts of MCM / waste FRP, 7 parts of compound resin base, 0.6 parts of flame retardant, and 2.5 parts of auxiliary additives.
[0028] in:
[0029] In MCM / waste FRP, the MCM material accounts for 10wt%, and the waste FRP accounts for 90wt%. During preparation, the waste FRP is first pulverized and blended with the MCM material, and...
Embodiment 2
[0035] The outer surface layer and the inner lining layer include the following components by weight: 35 parts of palygorskite / glass fiber composite fiber or its fabric containing zirconium phosphate, 12 parts of compound resin base, 1.3 parts of flame retardant, and 3 parts of auxiliary additives;
[0036] The structural layer includes the following components by weight: 30 parts of palygorskite / glass fiber composite fiber or its fabric containing zirconium phosphate, 7 parts of compound resin base, 0.5 part of borax, and 3 parts of auxiliary additives;
[0037] The MCM / waste FRP composite resin material includes the following components by weight: 25 parts of MCM / waste FRP, 5 parts of compound resin base, 0.6 part of flame retardant, and 1 part of auxiliary additive.
[0038] in:
[0039] The proportion of MCM material in MCM / waste glass fiber reinforced plastic is 8wt%, and the proportion of waste glass fiber reinforced plastic is 92wt%. During preparation, the waste glass ...
Embodiment 3
[0045] The outer surface layer and the inner lining layer include the following components by weight: 35 parts of palygorskite / glass fiber composite fiber or its fabric containing zirconium phosphate, 10 parts of compound resin base, 0.7 part of flame retardant, and 1 part of auxiliary additive;
[0046] The structural layer includes the following components by weight: 30 parts of palygorskite / glass fiber composite fiber or its fabric containing zirconium phosphate, 7 parts of compound resin base, 0.2 part of borax, and 1.5 part of auxiliary additive;
[0047] The MCM / waste FRP composite resin material includes the following components by weight: 25 parts of MCM / waste FRP, 3 parts of compound resin base, 0.7 part of flame retardant, and 0.5 part of auxiliary additive.
[0048] in:
[0049] The proportion of MCM material in MCM / waste FRP is 12wt%, and the proportion of waste FRP is 88wt%. During preparation, the waste FRP is crushed and blended with MCM material, and then hot-p...
PUM
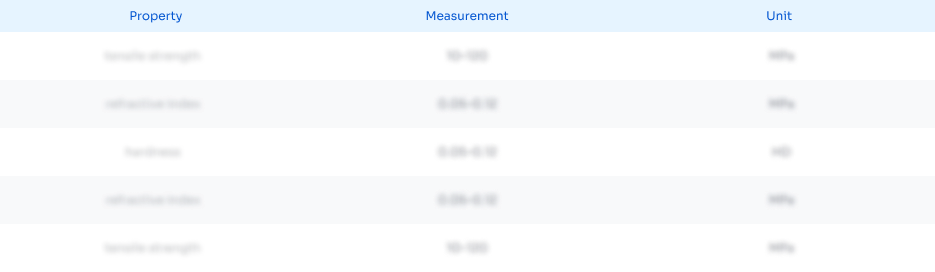
Abstract
Description
Claims
Application Information

- R&D
- Intellectual Property
- Life Sciences
- Materials
- Tech Scout
- Unparalleled Data Quality
- Higher Quality Content
- 60% Fewer Hallucinations
Browse by: Latest US Patents, China's latest patents, Technical Efficacy Thesaurus, Application Domain, Technology Topic, Popular Technical Reports.
© 2025 PatSnap. All rights reserved.Legal|Privacy policy|Modern Slavery Act Transparency Statement|Sitemap|About US| Contact US: help@patsnap.com