Bearing fault detection and diagnosis based on active learning
An active learning and fault detection technology, applied in the testing of mechanical components, testing of machine/structural components, measuring devices, etc., can solve the problems of low recognition rate of traditional methods
- Summary
- Abstract
- Description
- Claims
- Application Information
AI Technical Summary
Problems solved by technology
Method used
Image
Examples
Embodiment Construction
[0033] The present invention will be described in further detail below through specific embodiments in conjunction with the accompanying drawings. In the following detailed description, many detailed descriptions are for better understanding of the present invention, and those skilled in the art can clearly understand and understand. The content described below is illustrative rather than non-restrictive, and should not limit the protection scope of the present invention with this.
[0034] 1. Use the acquisition equipment for data acquisition. The test equipment has 4 sensors installed in different parts of the rolling bearing to record the vibration signal at the running time of the bearing. The sampling frequency of the sensor is f = 10KHZ, and the sampling time t = 1s, and the amplitude of the signal at different times is recorded value to get sampled data.
[0035] 2. Time-domain analysis is performed on the sampled data, that is, five time-domain factors are calculated a...
PUM
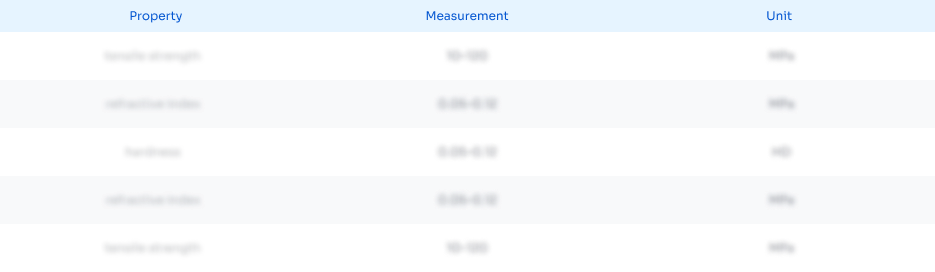
Abstract
Description
Claims
Application Information

- R&D Engineer
- R&D Manager
- IP Professional
- Industry Leading Data Capabilities
- Powerful AI technology
- Patent DNA Extraction
Browse by: Latest US Patents, China's latest patents, Technical Efficacy Thesaurus, Application Domain, Technology Topic, Popular Technical Reports.
© 2024 PatSnap. All rights reserved.Legal|Privacy policy|Modern Slavery Act Transparency Statement|Sitemap|About US| Contact US: help@patsnap.com