Machining fixing tool for special-shaped valve seat part
A technology for fixing tooling and valve seats, applied in positioning devices, metal processing equipment, metal processing machinery parts, etc., can solve problems affecting product quality and processing efficiency, large quantities, error accumulation, etc. The effect of shortening the process flow and reducing the number of tooling
- Summary
- Abstract
- Description
- Claims
- Application Information
AI Technical Summary
Problems solved by technology
Method used
Image
Examples
Embodiment 1
[0030] The structure of special-shaped valve seat part 4 in the prior art is as figure 1 and figure 2 As shown, its front features are two semicircular bosses 41, two threaded holes 42, part 4 large outer circle 43, part 4 back step outer circle 44 and two straight groove semicircles 45, the semicircular convex The platform 41 is in the same direction as the semicircle features of the two elevation angle curved surfaces 46 of the inner cavity of the part 4;
[0031] For the above-mentioned special-shaped valve seat part 4, this embodiment provides a processing and fixing tool for the special-shaped valve seat part, including a clamp base and a compression ring 1. Connected clamping part 2, the clamping part 2 is arranged on the positioning seat 3 at the end away from the part 4, and the front end of the positioning seat 3 is provided with a shallow groove that just accommodates two semicircular bosses 41 on the front of the part 4 32, the surface of the shallow groove 32 is...
Embodiment 2
[0034] As a preferred implementation mode, this embodiment provides a processing and fixing tool for special-shaped valve seat parts, such as image 3 and Figure 4 As shown, it includes a clamp base and a compression ring 1. The clamp base includes a positioning seat 3 and a clamping part 2 for connecting with the spindle chuck of the machine tool. The clamping part 2 is arranged on the positioning seat 3 away from the part 4 one end, the front end surface of the positioning seat 3 is provided with a shallow groove 32 that just accommodates the two semicircular bosses 41 on the front of the part 4, and the surface of the shallow groove 32 is provided with a positioning position corresponding to the threaded hole 42 on the part 4. Pin 6, the inner wall of the top of the compression ring sleeve 1 is provided with a circle of limit boss 12, the center of the limit boss 12 forms an opening that fits with the outer circle 44 of the step on the back of the part 4, and the compressi...
Embodiment 3
[0038] As the best implementation mode, this embodiment provides a processing fixture for special-shaped valve seat parts, including a clamp base and a compression ring 1, the clamp base includes a positioning seat 3 and is used to connect with the machine tool spindle chuck The clamping part 2, the clamping part 2 is set on the positioning seat 3 at the end away from the part 4, the front end of the positioning seat 3 is provided with a shallow groove 32 that just accommodates the two semicircular bosses 41 on the front of the part 4 , the surface of the shallow groove 32 is provided with a positioning pin 6 corresponding to the threaded hole 42 on the part 4, and the inner wall of the top end of the pressing ring 1 is provided with a circle of limiting bosses 12, and the center of the limiting boss 12 is An opening that fits in a gap with the outer circle 44 of the step on the back of the part 4 is formed, and the compression ring 1 and the positioning seat 3 are connected wi...
PUM
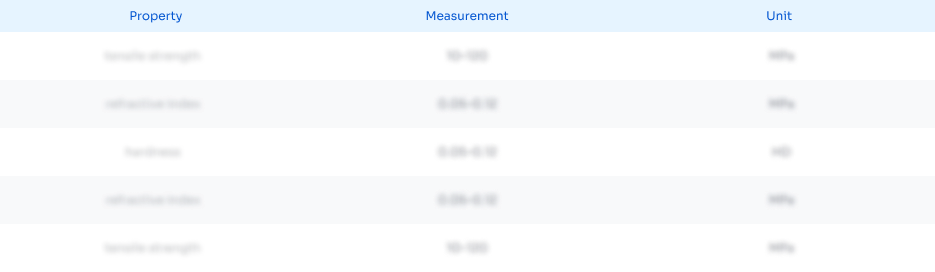
Abstract
Description
Claims
Application Information

- R&D Engineer
- R&D Manager
- IP Professional
- Industry Leading Data Capabilities
- Powerful AI technology
- Patent DNA Extraction
Browse by: Latest US Patents, China's latest patents, Technical Efficacy Thesaurus, Application Domain, Technology Topic, Popular Technical Reports.
© 2024 PatSnap. All rights reserved.Legal|Privacy policy|Modern Slavery Act Transparency Statement|Sitemap|About US| Contact US: help@patsnap.com