Variable-rigidity flexible mechanical arm
A technology of changing stiffness and fingers, applied in the field of manipulators, it can solve the problems of small change of elastic modulus and narrow range of stiffness change.
- Summary
- Abstract
- Description
- Claims
- Application Information
AI Technical Summary
Problems solved by technology
Method used
Image
Examples
Embodiment Construction
[0035] The present invention will be further described below in conjunction with specific examples and accompanying drawings.
[0036] A variable stiffness drive structure, such as figure 2 with image 3 As shown, the rotating structure 1 is included, and the two ends of the rotating structure 1 are respectively fixed with superelastic shape memory alloy wires, that is, the first superelastic shape memory alloy wire 2-1 and the second superelastic shape memory alloy wire 2-2. The structure 1 is covered with a bellows 3, and the bellows 3 is filled with a low melting point alloy. The two ends of the bellows 3 are sealed by a spring bracket, and the spring bracket is fixedly connected to the superelastic shape memory alloy wire. The first spring bracket 5 A shape memory alloy spring 4 is also fixed between -1 and the second spring bracket 5-2; by heating and cooling the low melting point alloy, the rotating structure 1 is switched between the rotating and locking states.
[0...
PUM
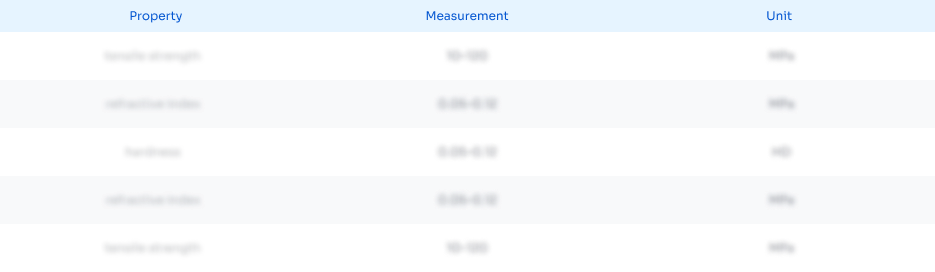
Abstract
Description
Claims
Application Information

- Generate Ideas
- Intellectual Property
- Life Sciences
- Materials
- Tech Scout
- Unparalleled Data Quality
- Higher Quality Content
- 60% Fewer Hallucinations
Browse by: Latest US Patents, China's latest patents, Technical Efficacy Thesaurus, Application Domain, Technology Topic, Popular Technical Reports.
© 2025 PatSnap. All rights reserved.Legal|Privacy policy|Modern Slavery Act Transparency Statement|Sitemap|About US| Contact US: help@patsnap.com