Method for stress monitoring of aircraft assembly process based on appearance detection
A technology for aircraft assembly and shape detection. It is applied in the direction of measuring force, measuring device, and optical device. It can solve problems such as lack of monitoring and parts deformation, and achieve the effect of improving assembly quality, prolonging aircraft life, and easy operation.
- Summary
- Abstract
- Description
- Claims
- Application Information
AI Technical Summary
Problems solved by technology
Method used
Examples
Embodiment 1
[0039] A method for monitoring stress in an aircraft assembly process based on shape detection, comprising:
[0040] Step S100: hoisting component A and component B into place;
[0041] Step S200: Set the public measurement points on the ground, establish the aircraft coordinate system and measure the key points of the shape of parts A and B respectively, and adjust the attitude of parts A and B according to the key points of the shape; after the attitude adjustment of parts A and B is completed The coordinates of the key points of the shape of the vehicle are used as the initial value, recorded to the initial data storage unit, and transmitted to the data operation unit together with the record of the sortie;
[0042] Step S300: fix component A, move component B along the course to approach component A, and perform pre-alignment of component A and component B;
[0043] Step S400: Trial assembly of the skeleton and skin of the transition section, monitor the process position ...
PUM
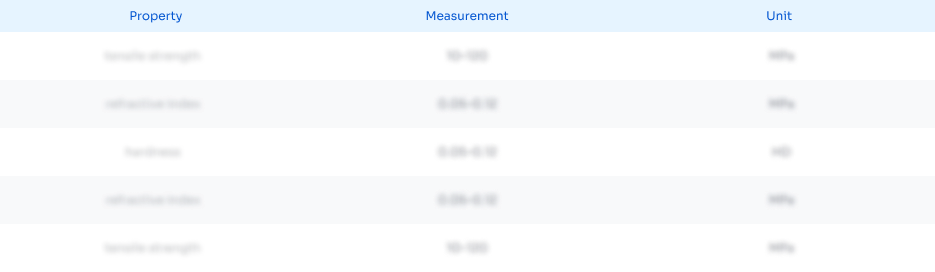
Abstract
Description
Claims
Application Information

- R&D
- Intellectual Property
- Life Sciences
- Materials
- Tech Scout
- Unparalleled Data Quality
- Higher Quality Content
- 60% Fewer Hallucinations
Browse by: Latest US Patents, China's latest patents, Technical Efficacy Thesaurus, Application Domain, Technology Topic, Popular Technical Reports.
© 2025 PatSnap. All rights reserved.Legal|Privacy policy|Modern Slavery Act Transparency Statement|Sitemap|About US| Contact US: help@patsnap.com