Preparation process of formed foil
A preparation process and technology of forming foil, which is applied in the direction of anodic oxidation, electrolytic coating, surface reaction electrolytic coating, etc., can solve the problems of poor water resistance, other performance effects, increased concentration, etc., and achieve high formation efficiency and water resistance Effects of performance change and improvement of formation efficiency
- Summary
- Abstract
- Description
- Claims
- Application Information
AI Technical Summary
Problems solved by technology
Method used
Examples
Embodiment 1
[0023] A preparation process of a chemically formed foil in this embodiment includes the following steps:
[0024] Step 1, aluminum foil pretreatment: put the aluminum foil in water at 100°C for 1 hour, then put it in salt solution for 20 minutes, then activate it, then wash it repeatedly with deionized water once, and then send it to the drying box Dry at 60°C for 30 minutes and set aside;
[0025] Step 2: Put the aluminum foil spared in Step 1 into the first-level chemical formation solution, then put it into the secondary chemical formation solution, and then pass through the DC battery. The DC battery voltage is 100V, and the formation time is 10 minutes, and then undergo preheating treatment 20 minutes, then add ammonium dihydrogen phosphate solidification solution to solidify for 8 minutes, and then dry in a 100°C drying oven for 1 hour.
[0026] The salt solution of this embodiment is a sodium chloride solution with a mass fraction of 40%.
[0027] In the activation t...
Embodiment 2
[0033] A preparation process of a chemically formed foil in this embodiment includes the following steps:
[0034] Step 1, aluminum foil pretreatment: put the aluminum foil in water at 100°C for 2 hours, then put it in salt solution for 30 minutes, then activate it, and then wash it repeatedly with deionized water for 3 times, then put it into the drying box Dry at 70°C for 40 minutes and set aside;
[0035] Step 2: Put the aluminum foil spared in Step 1 into the first-level chemical formation solution, then put it into the secondary chemical formation solution, and then pass it through a DC battery. The voltage of the DC battery is 200V, and the formation time is 15 minutes, and then it is preheated. After 30 minutes, add ammonium dihydrogen phosphate solidification solution to solidify for 12 minutes, and then dry in a 120°C drying oven for 2 hours.
[0036] The salt solution in this embodiment is a sodium chloride solution with a mass fraction of 50%.
[0037] In the acti...
Embodiment 3
[0043] A preparation process of a chemically formed foil in this embodiment includes the following steps:
[0044] Step 1, aluminum foil pretreatment: put the aluminum foil in water at 100°C for 1.5 hours, then put it in salt solution for 25 minutes, then activate it, then wash it twice with deionized water, and then send it to the drying box Dry at 65°C for 35 minutes and set aside;
[0045] Step 2: Put the aluminum foil spared in Step 1 into the first-level chemical formation solution, then put it into the secondary chemical formation solution, and then pass through the DC battery. The DC battery voltage is 150V, and the formation time is 12.5 minutes, and then preheated Treat for 25 minutes, then add ammonium dihydrogen phosphate solidification solution to solidify for 10 minutes, and then dry in a 110°C drying oven for 1.5 hours.
[0046] The salt solution of the present embodiment is a sodium chloride solution with a mass fraction of 45%.
[0047] In the activation trea...
PUM
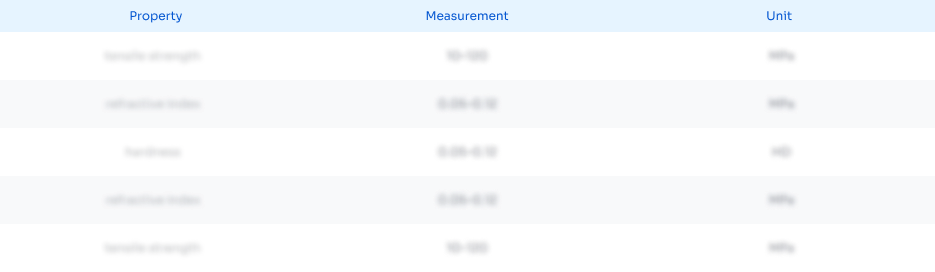
Abstract
Description
Claims
Application Information

- R&D
- Intellectual Property
- Life Sciences
- Materials
- Tech Scout
- Unparalleled Data Quality
- Higher Quality Content
- 60% Fewer Hallucinations
Browse by: Latest US Patents, China's latest patents, Technical Efficacy Thesaurus, Application Domain, Technology Topic, Popular Technical Reports.
© 2025 PatSnap. All rights reserved.Legal|Privacy policy|Modern Slavery Act Transparency Statement|Sitemap|About US| Contact US: help@patsnap.com