Refining method and device for alkylene oxide
A technology of alkylene oxide and refining method, which is applied in the direction of organic chemistry, can solve the problems of high cost, small processing capacity, troublesome adsorption and analysis process, etc., and achieve the effects of reducing energy consumption, improving the purity of the extractant, and increasing the yield
- Summary
- Abstract
- Description
- Claims
- Application Information
AI Technical Summary
Problems solved by technology
Method used
Image
Examples
Embodiment 1
[0108] according to figure 1 In the process flow shown, the extractant is n-octane, and the crude product stream containing 1,2-epoxybutane and the extractant stream containing n-octane enter the first rectification tower. In terms of molar percentage, the ratio of extractant to 1,2-epoxybutane is 8:1, the separation column reboiler E adopts a thermosiphon reboiler, and the extractant purifier F is a thermosiphon reboiler. The heat exchange area ratio of reboiler E and reboiler F is 5:1, and the part of the third stream entering the extractant purifier is 3% of the weight of the third stream.
[0109] The operating conditions of the first rectification tower are: pressure 0.042MPaG, tower top temperature 75°C.
[0110] The operating conditions of the second rectification tower are: pressure 0.04MPaG, tower top temperature 60°C.
[0111] The operating conditions of the separation tower are: pressure 0.04MPaG, tower top temperature 45°C.
[0112] The purity of the 1,2-butylen...
Embodiment 2
[0114] according to figure 1 In the process flow shown, the extractant is n-octane, and the crude product stream containing 1,2-epoxybutane and the extractant stream containing n-octane enter the first rectification tower. In terms of molar percentage, the ratio of extractant to 1,2-epoxybutane is 7:1, the separation tower reboiler E adopts a thermosiphon reboiler, and the extractant purifier F is a kettle-type reboiler, and then The heat exchange area ratio of the boiler E and the reboiler F is 5:1, and the part of the third stream entering the extractant purifier is 5% of the weight of the third stream.
[0115] The operating conditions of the first rectification tower are: pressure 0.10MPaG, tower top temperature 60°C.
[0116] The operating conditions of the second rectification tower are: pressure 0.09MPaG, tower top temperature 52°C.
[0117] The operating conditions of the separation tower are: pressure 0.09MPaG, tower top temperature 45°C.
[0118] The purity of the...
Embodiment 3
[0120] according to figure 1 In the process flow shown, the extractant is n-octane, and the crude product stream containing 1,2-epoxybutane and the extractant stream containing n-octane enter the first rectification tower. In terms of molar percentage, the ratio of extractant to 1,2-epoxybutane is 6:1, the separation tower reboiler E adopts a thermosyphon reboiler, and the extractant purifier F is a kettle-type reboiler, and then The heat exchange area ratio of the boiler E and the reboiler F is 5:1, and the part of the third stream entering the extractant purifier is 8% of the weight of the third stream.
[0121] The operating conditions of the first rectification tower are: pressure 0.20MPaG, tower top temperature 50°C.
[0122] The operating conditions of the second rectification tower are: pressure 0.19MPaG, tower top temperature 48°C.
[0123] The operating conditions of the separation tower are: pressure 0.18MPaG, tower top temperature 45°C.
[0124] The purity of the...
PUM
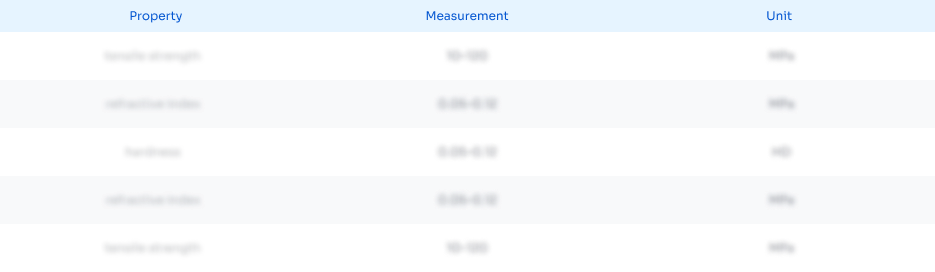
Abstract
Description
Claims
Application Information

- R&D Engineer
- R&D Manager
- IP Professional
- Industry Leading Data Capabilities
- Powerful AI technology
- Patent DNA Extraction
Browse by: Latest US Patents, China's latest patents, Technical Efficacy Thesaurus, Application Domain, Technology Topic, Popular Technical Reports.
© 2024 PatSnap. All rights reserved.Legal|Privacy policy|Modern Slavery Act Transparency Statement|Sitemap|About US| Contact US: help@patsnap.com