Method for sealing composite wing wall panel and metal wing rib based on co-bonding process
A technology of composite materials and co-gluing, which is applied in the direction of household components, household appliances, and other household appliances, can solve the problems of prolonging assembly time, increasing sealing difficulty, and increasing production costs, so as to reduce assembly processes, improve sealing effect, Effect of production cost reduction
- Summary
- Abstract
- Description
- Claims
- Application Information
AI Technical Summary
Problems solved by technology
Method used
Image
Examples
Embodiment Construction
[0030] Specific embodiments of the present invention will be described in detail below in conjunction with specific drawings. It should be noted that the technical features or combinations of technical features described in the following embodiments should not be regarded as isolated, and they can be combined with each other to achieve better technical effects. In the drawings of the following embodiments, the same reference numerals appearing in each drawing represent the same features or components, which can be applied in different embodiments.
[0031] The invention aims to solve the problems of cumbersome procedures and low efficiency in the prior art, which are caused by separate production of the sealing block and glue coating on all sides during sealing.
[0032] Such as Figure 4 , 5 As shown, the embodiment of the present invention is a method for sealing composite wing panels and metal ribs based on the co-gluing process, comprising the following steps: using glas...
PUM
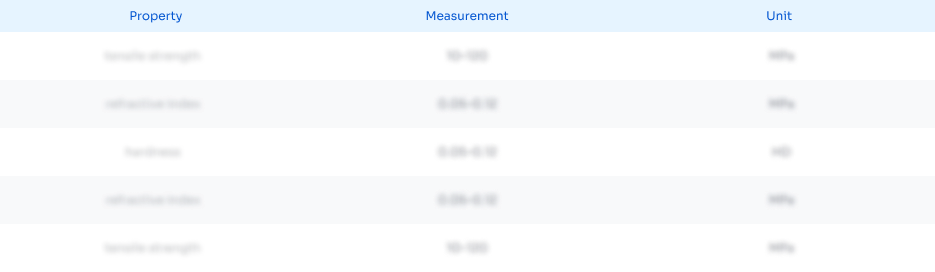
Abstract
Description
Claims
Application Information

- Generate Ideas
- Intellectual Property
- Life Sciences
- Materials
- Tech Scout
- Unparalleled Data Quality
- Higher Quality Content
- 60% Fewer Hallucinations
Browse by: Latest US Patents, China's latest patents, Technical Efficacy Thesaurus, Application Domain, Technology Topic, Popular Technical Reports.
© 2025 PatSnap. All rights reserved.Legal|Privacy policy|Modern Slavery Act Transparency Statement|Sitemap|About US| Contact US: help@patsnap.com