High-precision visual measurement method, device and system based on bionic algorithm
A visual measurement and high-precision technology, which is applied in the field of high-precision visual measurement based on bionic algorithms, can solve the problems of single-shot imaging field of view imaging accuracy constraints, and achieve the effect of improving efficiency and expanding the field of view
- Summary
- Abstract
- Description
- Claims
- Application Information
AI Technical Summary
Problems solved by technology
Method used
Image
Examples
Embodiment 1
[0075] see figure 1 As shown, the bionic algorithm-based high-precision visual measurement method provided by the present invention mainly includes steps:
[0076] Step S110, establishing a mapping relationship between the image pixel size and the actual spatial geometric size of the object to be measured.
[0077] This step is to establish the corresponding relationship between the coordinates of the pixel points in the image coordinate system and the coordinates of the target feature points of the measured object (such as a precision axis equiaxed set) in the world coordinate system. As a possible implementation manner, a reference image may be obtained in advance, and the correspondence relationship between the pixel size in the image and the actual spatial geometric size of the object to be measured can be established through the reference image.
[0078] Step S111, acquiring a plurality of first low-resolution images of the object to be measured.
[0079] Step S112, per...
Embodiment 2
[0087] Embodiment 2 of the present invention provides a preferred embodiment of a bionic algorithm-based high-precision visual measurement method.
[0088] In this embodiment, the method includes the steps of:
[0089] Step S211, acquiring a reference image, and establishing a mapping relationship between the pixel size in the reference image and the actual spatial geometric size of the object to be measured.
[0090] The reference image is a pre-acquired standard image, which is used to establish the correspondence between the pixel size of the image and the actual size of the object to be measured.
[0091] Preferably, before performing the measurement, it is also necessary to adjust the measurement accuracy of the imaging system from the perspective of hardware equipment. In the embodiment of the present invention, when the object plane moves along the optical axis of the system, a mathematical model is established to calculate the deflection angle between the optical axis...
Embodiment 3
[0212] The embodiment of the present invention also provides a high-precision visual measuring device based on a bionic algorithm. The unit includes:
[0213] The mapping module is used to obtain a reference image, and establish a mapping relationship between the pixel size in the reference image and the actual spatial geometric size of the object to be measured.
[0214] The image acquisition module is used to acquire multiple low-resolution images of the object to be measured.
[0215] The reconstruction module is used to perform super-resolution reconstruction based on the residual network on multiple low-resolution images to obtain the first super-resolution image.
[0216] The rough edge detection module is used for extracting edge points through an improved Canny edge detection operator for the first super-resolution image; and extracting corner points through Hilbert transform.
[0217] The fruit fly detection module is used to use edge points and corner points as heuri...
PUM
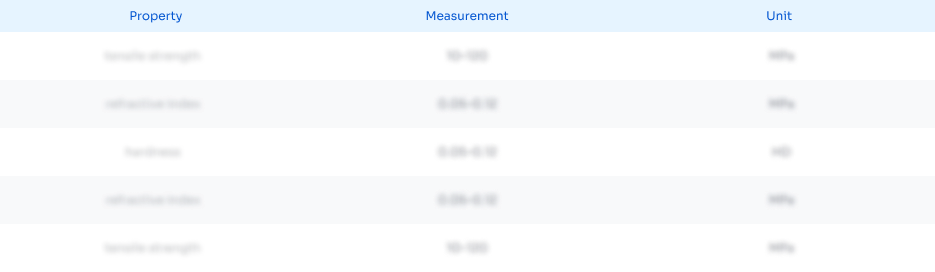
Abstract
Description
Claims
Application Information

- R&D
- Intellectual Property
- Life Sciences
- Materials
- Tech Scout
- Unparalleled Data Quality
- Higher Quality Content
- 60% Fewer Hallucinations
Browse by: Latest US Patents, China's latest patents, Technical Efficacy Thesaurus, Application Domain, Technology Topic, Popular Technical Reports.
© 2025 PatSnap. All rights reserved.Legal|Privacy policy|Modern Slavery Act Transparency Statement|Sitemap|About US| Contact US: help@patsnap.com