Bridge damage positioning method based on standing vehicle test
A damage location and damage location technology, which is applied in the analysis of solids by using sonic/ultrasonic/infrasonic waves, which can solve the problems of a large number of sensors, finite element models, and inconvenient implementation, so as to improve the localization efficiency, and the data analysis process is simple and applicable. sexual effect
- Summary
- Abstract
- Description
- Claims
- Application Information
AI Technical Summary
Problems solved by technology
Method used
Image
Examples
Embodiment 1
[0055] figure 2 The simply supported beam is shown with a length of 20m and a modulus of elasticity of 7.5×10 10 N / m 2 , with a density of 2.7 × 10 3 kg / m 3 , the cross section is a square section, the side length is 0.2m, and it is divided into 30 intervals at equal intervals. By means of numerical simulation, it is divided into 20 plane Euler beam elements for simulation, the sampling frequency is 100Hz, and the time is 200s. Using random excitation, the dynamic response of the beam is calculated by the Newmark-β method. This embodiment considers the following two working conditions:
[0056] (1) Single damage condition: interval 17, the section stiffness is reduced to 70% of the original value;
[0057] (2) Double damage condition: In interval 12, the section stiffness is reduced to 80% of the original value; in interval 20, the section stiffness is reduced to 75% of the original value.
[0058] Identification steps:
[0059] S1: Select a two-axle vehicle a with a ...
Embodiment 2
[0066] Figure 7 The two-span continuous beam cantilever beam shown, the length of each span is 15m, other parameters, solution method and identification process are the same as in Example 1, and two working conditions are also considered:
[0067] (1) Single damage condition: interval 23, the section stiffness is reduced to 80% of the original value;
[0068] (2) Double damage condition, in interval 10, the section stiffness is reduced to 70% of the original value, and in interval 23, the section stiffness is reduced to 75% of the original value. The positioning results under the single-damage condition and the double-damage condition are as follows: Figure 8 and Figure 9 shown.
[0069] Embodiments 1 and 2 verify that the method of the present invention adopts a single acceleration sensor for testing. By moving the position of the two-axle vehicle and measuring multiple system frequencies, damage localization can be effectively achieved through the constructed positioni...
PUM
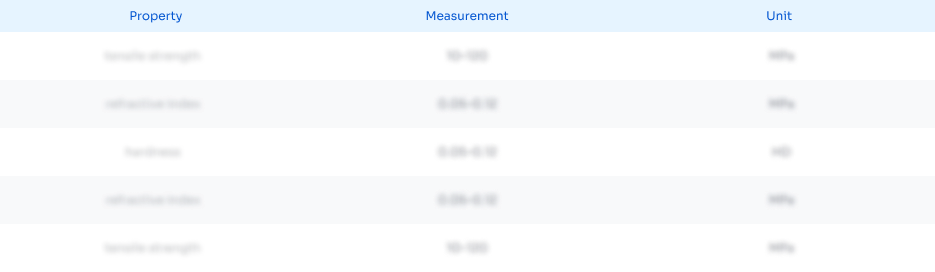
Abstract
Description
Claims
Application Information

- R&D Engineer
- R&D Manager
- IP Professional
- Industry Leading Data Capabilities
- Powerful AI technology
- Patent DNA Extraction
Browse by: Latest US Patents, China's latest patents, Technical Efficacy Thesaurus, Application Domain, Technology Topic, Popular Technical Reports.
© 2024 PatSnap. All rights reserved.Legal|Privacy policy|Modern Slavery Act Transparency Statement|Sitemap|About US| Contact US: help@patsnap.com