Preparation of Calcium Carbonate by Bubble Film Method and Its Application
A bubble film, calcium carbonate technology, applied in the direction of calcium carbonate/strontium/barium, nanotechnology for material and surface science, nanotechnology, etc., can solve the problems of uneven and stable product quality, long reaction time of calcium carbonate, etc. Achieve the effect of avoiding the reduction of the reaction rate, uniform and stable quality, good economic and social benefits
- Summary
- Abstract
- Description
- Claims
- Application Information
AI Technical Summary
Problems solved by technology
Method used
Image
Examples
Embodiment 1
[0031] A kind of bubble film method prepares calcium carbonate technology, comprises the following steps:
[0032] (1) Digestion: The medium-burned lime and hot water are poured into a rotary digester at a mass percentage ratio of 1:6 for digestion. The prepared calcium hydroxide emulsion is filtered through a 100-mesh vibrating screen to remove slag, and then passed through a rotary digester. Liquid separator further removes slag to obtain refined calcium hydroxide slurry, adjust the concentration of calcium hydroxide slurry to 12%, and age the refined calcium hydroxide slurry for 24 hours;
[0033] (2) Carbonization: pump the calcium hydroxide slurry prepared in step (1) into the carbonization reactor, the carbonization reactor is a gas dispersing disk with uniform and dense pores at the bottom, and the inside of the reactor is equipped with strong stirring The carbonization reaction device of the device; open the kiln gas valve and feed in the 2 The kiln gas with a volume ...
Embodiment 2
[0037] A kind of bubble film method prepares calcium carbonate technology, comprises the following steps:
[0038] (1) Digestion: The medium-burned lime and hot water are poured into a rotary digester at a mass percentage ratio of 1:5 for digestion. The prepared calcium hydroxide emulsion is filtered through an 80-mesh vibrating screen to remove slag, and then passed through a rotary digester. Liquid separator for further deslagging to obtain refined calcium hydroxide slurry, adjust the concentration of calcium hydroxide emulsion to 13%, and the refined calcium hydroxide slurry is not aged;
[0039] (2) Carbonization: pump the calcium hydroxide slurry prepared in step (1) into the carbonization reactor, the carbonization reactor is a gas dispersing disk with uniform and dense pores at the bottom, and the inside of the reactor is equipped with strong stirring The carbonization reaction device of the device; open the kiln gas valve and feed in the 2The kiln gas with a volume co...
Embodiment 3
[0043] A kind of bubble film method prepares calcium carbonate technology, comprises the following steps:
[0044] (1) Digestion: The medium-burned lime and hot water are poured into the rotary digester at a mass percentage ratio of 1:7 for digestion reaction. The prepared calcium hydroxide emulsion is filtered through a 100-mesh vibrating screen to remove slag, and then passed through a rotary digester. Liquid separator for further slag removal to obtain refined calcium hydroxide slurry, adjust the concentration of calcium hydroxide emulsion to 10%, and age the refined calcium hydroxide slurry for 36 hours;
[0045] (2) Carbonization: pump the calcium hydroxide slurry prepared in step (1) into the carbonization reactor, the carbonization reactor is a gas dispersing disk with uniform and dense pores at the bottom, and the inside of the reactor is equipped with strong stirring The carbonization reaction device of the device; open the kiln gas valve and feed in the 2 The kiln g...
PUM
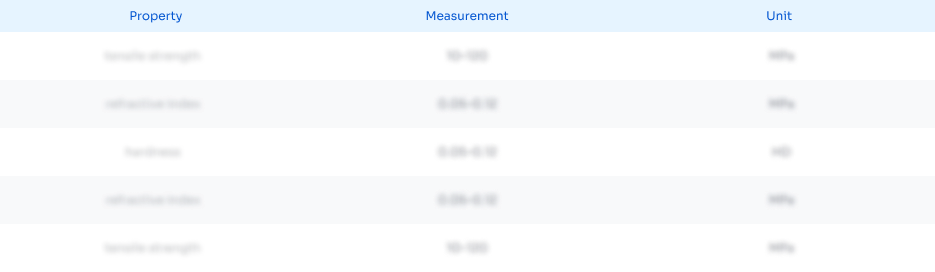
Abstract
Description
Claims
Application Information

- Generate Ideas
- Intellectual Property
- Life Sciences
- Materials
- Tech Scout
- Unparalleled Data Quality
- Higher Quality Content
- 60% Fewer Hallucinations
Browse by: Latest US Patents, China's latest patents, Technical Efficacy Thesaurus, Application Domain, Technology Topic, Popular Technical Reports.
© 2025 PatSnap. All rights reserved.Legal|Privacy policy|Modern Slavery Act Transparency Statement|Sitemap|About US| Contact US: help@patsnap.com