Roller type heat cutting-off mechanism
A thermal cutting, roll-type technology, applied in the direction of object supply, electrolyte battery manufacturing, sustainable manufacturing/processing, etc., can solve problems such as inability to cut, temperature drop, etc., and achieve the effect of preventing re-adhesion
- Summary
- Abstract
- Description
- Claims
- Application Information
AI Technical Summary
Problems solved by technology
Method used
Image
Examples
Embodiment Construction
[0026] In order to fully understand the technical content of the present invention, the technical solutions of the present invention will be further introduced and illustrated below in conjunction with specific examples, but not limited thereto.
[0027] Such as Figure 1 to Figure 3 As shown, a roller thermal cut-off mechanism includes a feed roller 10, a feed power device 20, a discharge roller 30 and a discharge power device 40, the feed roller 10 is connected with the feed power device 20, and the discharge roller 30 is connected with the discharge power device 40, the feed roller 10 is provided with a thermal cutting wire 50, the discharge roller 30 is arranged in front of the feed roller 10, the first lamination unit 61 enters the feed roller 10 and Driven by the roller 10, it advances to the discharge roller 30. After the first lamination unit 61 passes through the feed roller 10 completely, the thermal cutting wire 50 cuts off the diaphragm 63 connected between the two...
PUM
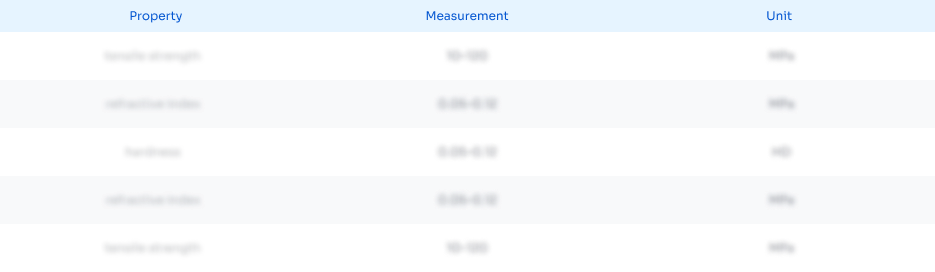
Abstract
Description
Claims
Application Information

- Generate Ideas
- Intellectual Property
- Life Sciences
- Materials
- Tech Scout
- Unparalleled Data Quality
- Higher Quality Content
- 60% Fewer Hallucinations
Browse by: Latest US Patents, China's latest patents, Technical Efficacy Thesaurus, Application Domain, Technology Topic, Popular Technical Reports.
© 2025 PatSnap. All rights reserved.Legal|Privacy policy|Modern Slavery Act Transparency Statement|Sitemap|About US| Contact US: help@patsnap.com