Real-time correction method for rotor time constant of three-phase asynchronous motor
A technology of rotor time constant and motor rotor, which is applied to control generator, motor generator control, electronic commutation motor control, etc. The effect of improving orientation accuracy
- Summary
- Abstract
- Description
- Claims
- Application Information
AI Technical Summary
Problems solved by technology
Method used
Image
Examples
Embodiment Construction
[0038]Specific embodiments of the present invention will be further described below in conjunction with the accompanying drawings.
[0039] The present invention aims at the defects of poor engineering practice existing in methods such as self-adaptive filtering, Kalman filtering, least square method, and neural network for rotor time constant identification in the prior art, and proposes a simple and practical three-phase asynchronous motor Real-time correction method of rotor time constant. Generally, when the motor leaves the factory, the manufacturer provides the excitation mutual inductance curve (the relationship curve between the excitation mutual inductance and the excitation current) and the rotor resistance temperature curve (the relationship curve between the rotor resistance and the rotor temperature), or the motor parameter identification based on the vector control based on the rotor field orientation can be used. The method measures the excitation mutual inducta...
PUM
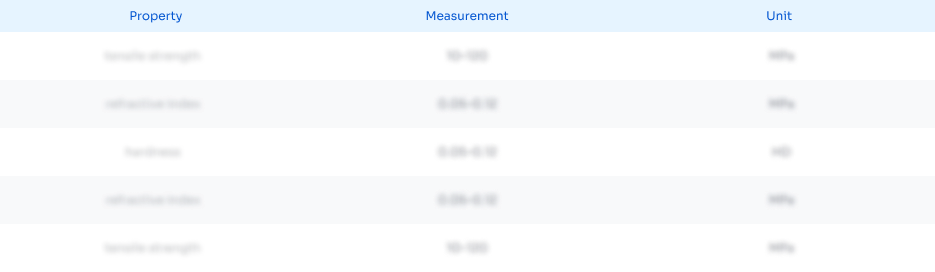
Abstract
Description
Claims
Application Information

- R&D
- Intellectual Property
- Life Sciences
- Materials
- Tech Scout
- Unparalleled Data Quality
- Higher Quality Content
- 60% Fewer Hallucinations
Browse by: Latest US Patents, China's latest patents, Technical Efficacy Thesaurus, Application Domain, Technology Topic, Popular Technical Reports.
© 2025 PatSnap. All rights reserved.Legal|Privacy policy|Modern Slavery Act Transparency Statement|Sitemap|About US| Contact US: help@patsnap.com