Printing dye formula and production process thereof
A production process and dye technology, applied in inks, household appliances, applications, etc., to improve friction resistance and fluidity, maintain efficacy, and improve wetting performance.
- Summary
- Abstract
- Description
- Claims
- Application Information
AI Technical Summary
Problems solved by technology
Method used
Examples
Embodiment 1
[0019] Embodiment 1: The present invention provides a technical solution: a printing dye formulation and its production process. The main components of the printing dye are composed of the following parts by weight: 35-45 parts of acrylic resin, 15 parts of amino resin dye, and oil dilution 10 parts of solvent (oligomeric linseed oil), 3 parts of slip agent (microcrystalline wax), 5 parts of colorant (cadmium red), 0.2 part of surfactant, 1 part of ethanol, 5 parts of deionized water, 0.5 part of filler (Barium sulfate) and 0.3 parts of defoamer.
[0020] In the present invention: the production technique of printing dye is as follows:
[0021] Step 1: Material preparation: Measure acrylic resin, amino resin dye, oil dilution solvent, slip agent, colorant, dispersant, ethanol, and filler according to the above parts by weight, and then measure the above components. placed in a fume hood for use;
[0022] Step 2: Ingredients: Take out the pre-prepared raw materials in the fum...
Embodiment 2
[0029] Embodiment 2: The difference between this embodiment and Embodiment 1 is:
[0030] A printing dye formulation and a production process thereof. The main components of the printing dye are composed of the following parts by weight: 45 parts of acrylic resin, 25 parts of amino resin dye, 15 parts of oil dilution solvent (oligomerized linseed oil), 5 parts of slip agent (synthetic wax), 9 parts of colorant (chrome green), 0.6 part of surfactant, 3 parts of ethanol, 7 parts of deionized water, 0.8 part of filler (talc) and 0.8 part of defoamer.
[0031] In the present invention: the production technique of printing dye is as follows:
[0032] Step 1: Material preparation: Measure acrylic resin, amino resin dye, oil dilution solvent, slip agent, colorant, dispersant, ethanol, and filler according to the above parts by weight, and then measure the above components. placed in a fume hood for use;
[0033] Step 2: Ingredients: Take out the pre-prepared raw materials in the fu...
Embodiment 3
[0040] Embodiment 3: The difference between this embodiment and Embodiment 1 and Embodiment 2 is:
[0041] A printing dye formulation and a production process thereof. The main components of the printing dye are composed of the following parts by weight: 40 parts of acrylic resin, 22 parts of amino resin dye, 13 parts of oil dilution solvent (oligomerized linseed oil), and 3.5 parts of slip agent parts (synthetic wax), 7 parts of colorant (ultramarine blue), 0.4 parts of surfactant, 2.5 parts of ethanol, 5.5 parts of deionized water, 0.65 parts of filler (aluminum hydroxide) and 0.5 part of defoamer.
[0042] In the present invention: the production technique of printing dye is as follows:
[0043] Step 1: Material preparation: Measure acrylic resin, amino resin dye, oil dilution solvent, slip agent, colorant, dispersant, ethanol, and filler according to the above parts by weight, and then measure the above components. placed in a fume hood for use;
[0044] Step 2: Ingredie...
PUM
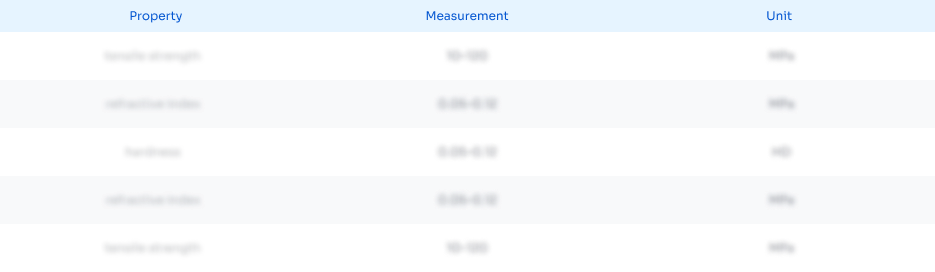
Abstract
Description
Claims
Application Information

- R&D
- Intellectual Property
- Life Sciences
- Materials
- Tech Scout
- Unparalleled Data Quality
- Higher Quality Content
- 60% Fewer Hallucinations
Browse by: Latest US Patents, China's latest patents, Technical Efficacy Thesaurus, Application Domain, Technology Topic, Popular Technical Reports.
© 2025 PatSnap. All rights reserved.Legal|Privacy policy|Modern Slavery Act Transparency Statement|Sitemap|About US| Contact US: help@patsnap.com