Spinning manufacturing method for shell body
A manufacturing method and spinning technology, applied in the field of mechanical processing, can solve problems such as difficulty in taking into account manufacturing accuracy, cost, and production efficiency, environmental compliance, etc., and achieve environmental protection and occupational health. Effect
- Summary
- Abstract
- Description
- Claims
- Application Information
AI Technical Summary
Problems solved by technology
Method used
Image
Examples
Embodiment 1
[0029] Embodiment 1 discloses a spinning manufacturing method of a shell, including the following processing steps:
[0030] A. Select the plate as the raw material, and put down the circular spinning blank 100, and punch the center positioning hole, such as figure 1 shown;
[0031] B. If figure 2 and image 3 As shown, the first ejector block 12 is installed on the first lower spinning die base 11 of the powerful spinning machine, and the spinning blank 100 obtained in step A is fixed on the first lower spinning die base 11 and connected to the first lower spinning die base 11. The ejector block 12 is coaxial, and the first upper adapter seat 13 presses the spinning blank; the main shaft of the powerful spinning machine is rotated, and the main shaft of the powerful spinning machine drives the first spinning lower mold base 11 and the spinning blank 100 1. The first ejector block 12 and the first upper adapter seat 13 rotate together; the first shoveling wheel 14 of the p...
Embodiment 2
[0041] Embodiment 2 discloses a spinning manufacturing method of a casing, including the following processing steps:
[0042] A. Select the plate as the raw material, lower the circular spinning blank 100, and punch the center positioning hole;
[0043] B. Install the first ejector block 12 on the first lower die base 11 of the powerful spinning machine, fix the spinning blank 100 obtained in step A on the lower die base 11 of the first spinning and connect it with the first ejector The material block 12 is coaxial, and the first upper adapter seat 13 presses the spinning blank; the main shaft of the powerful spinning machine is allowed to rotate, and the main shaft of the powerful spinning machine drives the first spinning lower mold base 11, the spinning blank 100, The first ejector block 12 and the first upper adapter seat 13 rotate together; use the first shovel wheel 14 of the powerful spinning machine to move radially along the upper surface of the spinning blank 100 acc...
Embodiment 3
[0053] Embodiment 3 discloses a spinning manufacturing method of a shell, including the following processing steps:
[0054] A. Select the plate as the raw material, lower the circular spinning blank 100, and punch the center positioning hole;
[0055] B. Install the first ejector block 12 on the first lower die base 11 of the powerful spinning machine, fix the spinning blank 100 obtained in step A on the lower die base 11 of the first spinning and connect it with the first ejector The material block 12 is coaxial, and the first upper adapter seat 13 presses the spinning blank; the main shaft of the powerful spinning machine is allowed to rotate, and the main shaft of the powerful spinning machine drives the first spinning lower mold base 11, the spinning blank 100, The first ejector block 12 and the first upper adapter seat 13 rotate together; use the first shovel wheel 14 of the powerful spinning machine to move radially along the upper surface of the spinning blank 100 acco...
PUM
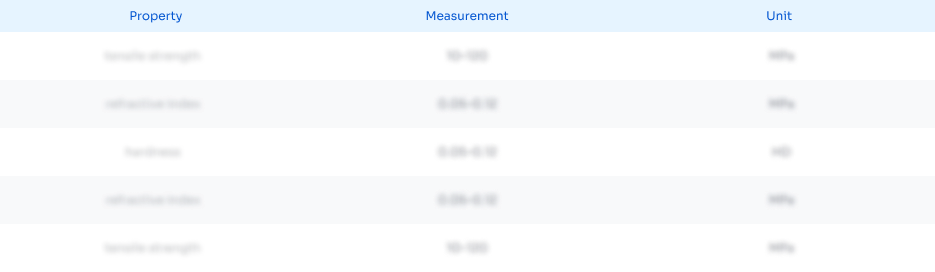
Abstract
Description
Claims
Application Information

- R&D
- Intellectual Property
- Life Sciences
- Materials
- Tech Scout
- Unparalleled Data Quality
- Higher Quality Content
- 60% Fewer Hallucinations
Browse by: Latest US Patents, China's latest patents, Technical Efficacy Thesaurus, Application Domain, Technology Topic, Popular Technical Reports.
© 2025 PatSnap. All rights reserved.Legal|Privacy policy|Modern Slavery Act Transparency Statement|Sitemap|About US| Contact US: help@patsnap.com