A monocular vision-based gravitational field method accelerometer calibration method
An accelerometer and monocular vision technology, which is used in the testing/calibration, speed/acceleration/impact measurement, and calculation of speed/acceleration/shock measurement equipment, etc. The effect of low cost and simple calibration process
- Summary
- Abstract
- Description
- Claims
- Application Information
AI Technical Summary
Problems solved by technology
Method used
Image
Examples
Embodiment Construction
[0046] In order to solve the problem that the existing gravitational field method accelerometer has limited calibration accuracy and is only applicable to the two-point method single-axis accelerometer calibration, the present invention provides a gravity field method accelerometer calibration method based on monocular vision, which improves the accuracy of the gravitational field method. The calibration accuracy and applicability of the accelerometer calibration will be described in detail below in conjunction with the accompanying drawings and specific implementation examples.
[0047] refer to figure 1It is a schematic diagram of an implementation example device of the method of the present invention, which mainly includes: a circular turntable 1, a rectangular target 2, a low-frequency acceleration sensor 3, an imaging device fixing device 4, an imaging and acquisition device 5, a plumb line fixing device 6 and a plumb weight and vertical line 7. The circular turntable 1 ...
PUM
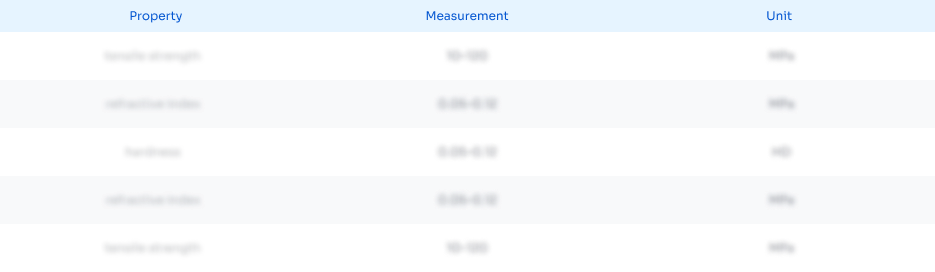
Abstract
Description
Claims
Application Information

- R&D
- Intellectual Property
- Life Sciences
- Materials
- Tech Scout
- Unparalleled Data Quality
- Higher Quality Content
- 60% Fewer Hallucinations
Browse by: Latest US Patents, China's latest patents, Technical Efficacy Thesaurus, Application Domain, Technology Topic, Popular Technical Reports.
© 2025 PatSnap. All rights reserved.Legal|Privacy policy|Modern Slavery Act Transparency Statement|Sitemap|About US| Contact US: help@patsnap.com