Aluminum silicon carbide tube shell electrical insulator and sintering method thereof
The technology of a silicon carbide tube and a sintering method is applied in the field of aluminum silicon carbide tube shell insulators and its sintering, and can solve the problems of sintering insulators that are not suitable for aluminum silicon carbide tube shells, difficult to weld insulators, and materials that are not resistant to high temperature. The effect of solving the problem of difficult sintering, low crack tendency and no pollution
- Summary
- Abstract
- Description
- Claims
- Application Information
AI Technical Summary
Problems solved by technology
Method used
Image
Examples
Embodiment 1
[0040] S1. Place the aluminum silicon carbide shell with holes designed in advance on a custom mold mixed with stainless steel and graphite, and the limited slot on the mold can fix the shell;
[0041] S2. Put the self-made glass powder hollow tube on the hole of the tube shell, and insert the Kovar lead wire in the middle;
[0042] S3. Separate the two ends of the hole with graphite paper, and then fill the hole with carbon powder to ensure that the carbon powder can completely bury the hole;
[0043] S4. Put the mold together with the shell into the self-made microwave sintering furnace, adjust the microwave output power to 100W, and the sintering time to 60min, and start the sintering by running the program;
[0044] S5. After sintering, take out the shell, clean the surface, and complete the sintering of the insulator. The lead wire and the aluminum silicon carbide shell are well welded through insulating glass, and the airtightness is less than 10 -10 Pa·m 3 / s, meet th...
Embodiment 2
[0046] S1. Place the aluminum silicon carbide shell with holes designed in advance on a custom mold mixed with stainless steel and graphite, and the limited slot on the mold can fix the shell;
[0047] S2. Put the self-made glass powder hollow tube on the hole of the tube shell, and insert the Kovar lead wire in the middle;
[0048] S3. Separate the two ends of the hole with graphite paper, and then fill the hole with carbon powder to ensure that the carbon powder can completely bury the hole;
[0049] S4. Put the mold together with the shell into the self-made microwave sintering furnace, adjust the microwave output power to 10KW, the sintering time to 10min, and start the sintering with the operating program;
[0050] S5. After sintering, take out the shell, clean the surface, and complete the sintering of the insulator. The lead wire and the AlSiC shell are well welded by insulating glass, and the airtightness is less than 10 -10 Pa·m 3 / s, meet the national military standa...
Embodiment 3
[0052] S1. Place the aluminum silicon carbide shell with holes designed in advance on a custom mold mixed with stainless steel and graphite, and the limited slot on the mold can fix the shell;
[0053] S2. Put the self-made glass powder hollow tube on the hole of the tube shell, and insert the Kovar lead wire in the middle;
[0054] S3. Separate the two ends of the hole with graphite paper, and then fill the hole with carbon powder to ensure that the carbon powder can completely bury the hole;
[0055] S4. Put the mold together with the shell into the self-made microwave sintering furnace, adjust the microwave output power to 5000W, the sintering time to 30min, and start the sintering with the running program;
[0056] S5. After sintering, take out the shell, clean the surface, and complete the sintering of the insulator. The lead wire and the AlSiC shell are well welded by insulating glass, and the airtightness is less than 10 -10 Pa·m 3 / s, meet the national military stand...
PUM
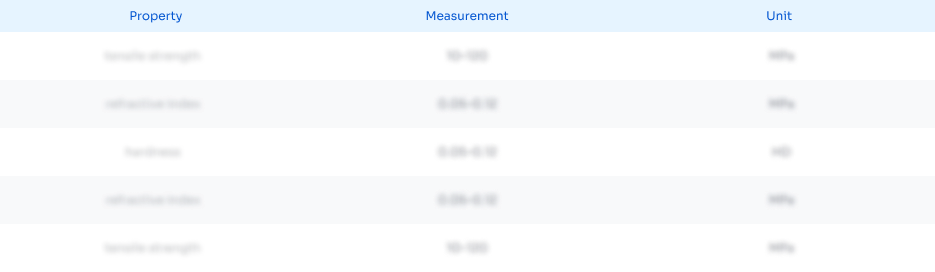
Abstract
Description
Claims
Application Information

- R&D
- Intellectual Property
- Life Sciences
- Materials
- Tech Scout
- Unparalleled Data Quality
- Higher Quality Content
- 60% Fewer Hallucinations
Browse by: Latest US Patents, China's latest patents, Technical Efficacy Thesaurus, Application Domain, Technology Topic, Popular Technical Reports.
© 2025 PatSnap. All rights reserved.Legal|Privacy policy|Modern Slavery Act Transparency Statement|Sitemap|About US| Contact US: help@patsnap.com