Involute harmonic gear shaping method and harmonic reducer
A harmonic gear and involute technology, applied in the direction of belts/chains/gears, mechanical equipment, transmission devices, etc., can solve problems such as poor meshing effect, difficult tooth shape processing, easy interference, etc., to improve meshing quality, Improve the effect of stress situation and avoid interference
- Summary
- Abstract
- Description
- Claims
- Application Information
AI Technical Summary
Problems solved by technology
Method used
Image
Examples
Embodiment Construction
[0057] Below, the present invention will be further described in conjunction with the accompanying drawings and specific implementation methods. It should be noted that, under the premise of not conflicting, the various embodiments described below or the technical features can be combined arbitrarily to form new embodiments. .
[0058] Such as Figure 1-5 As shown, the modification method of the involute harmonic gear, the harmonic gear includes the flexible spline 2 and the rigid spline 1, the modification method includes the following modification steps,
[0059] A) Modification steps of flexspline 2:
[0060] (1) Calculate the gear modulus m of flexspline 2 by the following formula r ,
[0061] m r =(d rn +2δ r ) / [Z r -2(h ra +c r )],
[0062] Among them, Z r is the number of teeth of the flex spline, h ra is the addendum height coefficient of the flexible spline, c r is the flexspline head clearance coefficient, d rn is the inner hole diameter of flexspline g...
PUM
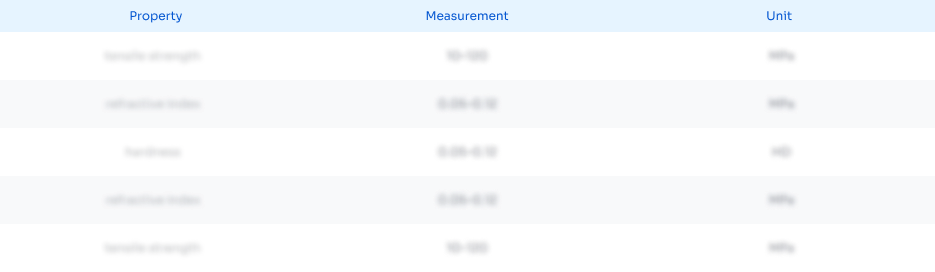
Abstract
Description
Claims
Application Information

- R&D Engineer
- R&D Manager
- IP Professional
- Industry Leading Data Capabilities
- Powerful AI technology
- Patent DNA Extraction
Browse by: Latest US Patents, China's latest patents, Technical Efficacy Thesaurus, Application Domain, Technology Topic, Popular Technical Reports.
© 2024 PatSnap. All rights reserved.Legal|Privacy policy|Modern Slavery Act Transparency Statement|Sitemap|About US| Contact US: help@patsnap.com