Fiber laser and laser material processing system
A fiber laser, fiber laser technology, applied in lasers, laser parts, phonon exciters, etc., can solve the problems of complex manufacturing coupling process, high implementation cost, ring-core multi-clad fiber, etc., to achieve cross-sectional characteristics, The production process is simple and the effect of change is achieved
- Summary
- Abstract
- Description
- Claims
- Application Information
AI Technical Summary
Problems solved by technology
Method used
Image
Examples
Embodiment 1
[0064] Please refer to figure 1 and figure 2 As shown, a fiber laser is provided for this embodiment, and seven cylindrical light guide columns 4 are closely arranged in a circle, that is, there is one light guide column 4 in the middle, and the other six light guide columns 4 surround the middle light guide column 4 tightly in the circumferential direction. Arrangement, the pigtails of the seven light guide columns 4 can be connected to different fiber laser modules 1, or some of the pigtails of the light guide columns 4 can be connected to a certain fiber laser module 1, and the laser power of each fiber laser module 1 can be respectively The control can also control several or all of them synchronously, so as to realize the change or control of the characteristics of the output spot.
[0065] For example, the output laser power of the middle light guide column 4 can be individually controlled, and at the same time, the output laser power of the six light guide columns 4 i...
Embodiment 2
[0067] refer to image 3 and Figure 4 As shown, another fiber laser is provided for this embodiment, which includes three fiber laser modules 1, wherein two fiber laser modules 1 are connected to a secondary light guide column, and the other fiber laser module 1 is connected to the main light column. The fiber laser of this embodiment adds auxiliary light guide columns around or next to the main light column, which can reduce spatter and homogenize the molten pool, so the output beam of the fiber laser can effectively improve the welding effect.
Embodiment 3
[0069] refer to Figure 5 As shown, another fiber laser provided in this embodiment includes seven fiber laser modules 1 , and each fiber laser module 1 is connected to a light guide column 4 .
PUM
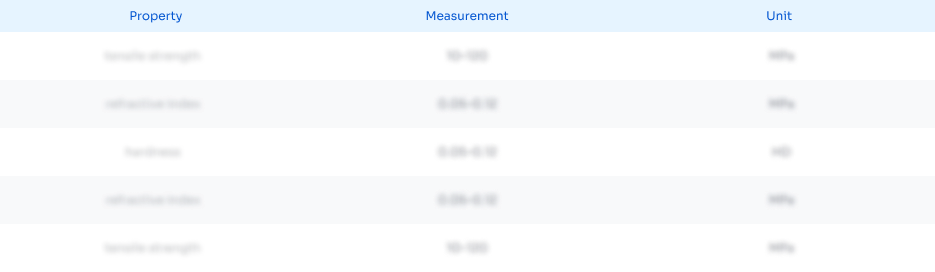
Abstract
Description
Claims
Application Information

- R&D
- Intellectual Property
- Life Sciences
- Materials
- Tech Scout
- Unparalleled Data Quality
- Higher Quality Content
- 60% Fewer Hallucinations
Browse by: Latest US Patents, China's latest patents, Technical Efficacy Thesaurus, Application Domain, Technology Topic, Popular Technical Reports.
© 2025 PatSnap. All rights reserved.Legal|Privacy policy|Modern Slavery Act Transparency Statement|Sitemap|About US| Contact US: help@patsnap.com