Manufacturing method for multi-components superfine mask cloth
A manufacturing method and multi-component technology, applied in the direction of non-woven fabrics, textiles and papermaking, etc., can solve the problems of mask elasticity, hand feeling comfort and poor fit, and achieve good skin adhesion, fine cloth surface, and increased absorption Effect
- Summary
- Abstract
- Description
- Claims
- Application Information
AI Technical Summary
Problems solved by technology
Method used
Examples
Embodiment Construction
[0007] The technical solutions in the embodiments of the present invention will be clearly and completely described below in conjunction with the embodiments of the present invention. Apparently, the described embodiments are only some of the embodiments of the present invention, not all of them. Based on the embodiments of the present invention, all other embodiments obtained by persons of ordinary skill in the art without making creative efforts belong to the protection scope of the present invention.
[0008] A kind of manufacture method of multi-component ultra-fine mask cloth comprises the following steps: (1) PA-6 polymer slice, PET polymer slice and PLA polymer slice are respectively crystallized and dried, melt-extruded, and pre-filtered to obtain The molten body is measured by a measuring vessel, and injected into the multi-component spinning hole according to the ratio of pressure, and the multi-component composite as-spun silk is obtained under a certain temperature ...
PUM
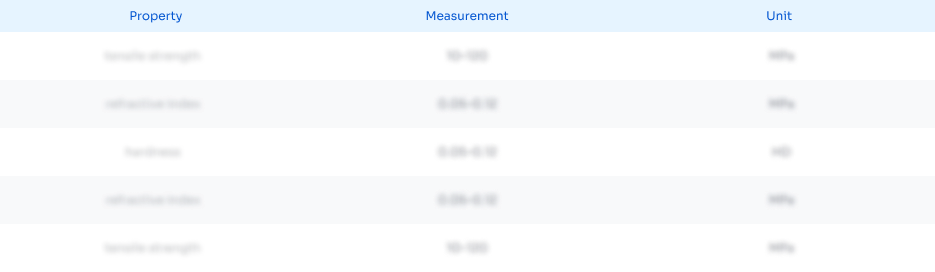
Abstract
Description
Claims
Application Information

- Generate Ideas
- Intellectual Property
- Life Sciences
- Materials
- Tech Scout
- Unparalleled Data Quality
- Higher Quality Content
- 60% Fewer Hallucinations
Browse by: Latest US Patents, China's latest patents, Technical Efficacy Thesaurus, Application Domain, Technology Topic, Popular Technical Reports.
© 2025 PatSnap. All rights reserved.Legal|Privacy policy|Modern Slavery Act Transparency Statement|Sitemap|About US| Contact US: help@patsnap.com