A force and rigidity equivalence-based head car mold shrinkage construction method and a head car mold shrinkage
A head car and stiffness technology, which is applied in the field of head car reduction, can solve the problems of changing the center of gravity of the train, difficult to simulate accurately, and the impact of train collision dynamic response is large, and achieves the effect of high reliability and structural similarity.
- Summary
- Abstract
- Description
- Claims
- Application Information
AI Technical Summary
Problems solved by technology
Method used
Image
Examples
Embodiment Construction
[0087] The present invention will be further described below in conjunction with examples.
[0088] Such as figure 1 As shown, a kind of locomotive shrinkage model construction method based on force and stiffness equivalent provided by the present invention mainly includes the following four aspects:
[0089] 1. Similarity factor derivation of kinetic parameters;
[0090] 2. Partition design of the first car;
[0091] 3. Build the initial reduced model of the head car;
[0092] 4. The collision simulation calculation of the shrinking mold of the head car and the optimization of the shrinking mold of the head car.
[0093] 1. The similarity factor derivation about the dynamic parameters: the present invention considers that the train is a thin-walled aluminum alloy structure, so the similarity relationship of its dynamic characteristics is analyzed for the thin-walled plate shell, that is, the dynamic balance equation based on the thin-walled plate shell adopts similarity T...
PUM
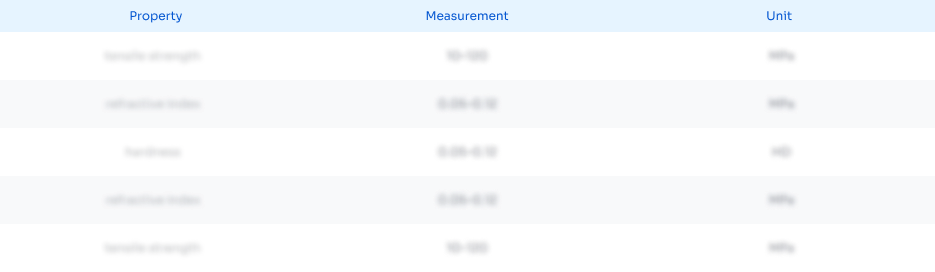
Abstract
Description
Claims
Application Information

- Generate Ideas
- Intellectual Property
- Life Sciences
- Materials
- Tech Scout
- Unparalleled Data Quality
- Higher Quality Content
- 60% Fewer Hallucinations
Browse by: Latest US Patents, China's latest patents, Technical Efficacy Thesaurus, Application Domain, Technology Topic, Popular Technical Reports.
© 2025 PatSnap. All rights reserved.Legal|Privacy policy|Modern Slavery Act Transparency Statement|Sitemap|About US| Contact US: help@patsnap.com