A casting and forging composite forming device for shaft sleeve parts
A technology of parts and shaft sleeves, which is applied in the field of casting and forging composite forming devices, can solve the problems of small application range and achieve the effects of improving production efficiency, reducing equipment occupation, and shortening the process flow
- Summary
- Abstract
- Description
- Claims
- Application Information
AI Technical Summary
Problems solved by technology
Method used
Image
Examples
Embodiment 1
[0031] Such as Figures 1 to 5 As shown, the casting and forging compound forming device of the shaft sleeve parts includes a casting module located in the middle, a forging module 1 located on both sides, a temperature monitoring device and an extruder workbench 14, and the top of the extruder workbench 14 is set There is a casting module, the casting module includes the casting mold upper mold 2, the casting mold lower mold 11 and the extrusion punch 13 in the bottom injection hydraulic press, the forging module 1 includes a push-pull device, a rotating device and a special core, and the push-pull device includes a compression cylinder 7. The rotating device includes a special core 3, a rotating rod 4, a reduction transmission box 5 and a motor 6, and the temperature monitoring device includes a temperature recorder 9 and a temperature measuring thermocouple 10;
[0032] In the casting module, the casting mold upper mold 2 is provided with a lifting structure, the casting mo...
Embodiment 2
[0040] Such as Figures 1 to 5As shown, the casting and forging compound forming device of the shaft sleeve parts includes a casting module located in the middle, a forging module 1 located on both sides, a temperature monitoring device and an extruder workbench 14, and the top of the extruder workbench 14 is set There is a casting module, the casting module includes the casting mold upper mold 2, the casting mold lower mold 11 and the extrusion punch 13 in the bottom injection hydraulic press, the forging module 1 includes a push-pull device, a rotating device and a special core, and the push-pull device includes a compression cylinder 7. The rotating device includes a special core 3, a rotating rod 4, a reduction transmission box 5 and a motor 6, and the temperature monitoring device includes a temperature recorder 9 and a temperature measuring thermocouple 10;
[0041] In the casting module, the casting mold upper mold 2 is provided with a lifting structure, the casting mol...
Embodiment 3
[0049] Such as Figures 1 to 5 As shown, the casting and forging compound forming device of the shaft sleeve parts includes a casting module located in the middle, a forging module 1 located on both sides, a temperature monitoring device and an extruder workbench 14, and the top of the extruder workbench 14 is set There is a casting module, the casting module includes the casting mold upper mold 2, the casting mold lower mold 11 and the extrusion punch 13 in the bottom injection hydraulic press, the forging module 1 includes a push-pull device, a rotating device and a special core, and the push-pull device includes a compression cylinder 7. The rotating device includes a special core 3, a rotating rod 4, a reduction transmission box 5 and a motor 6, and the temperature monitoring device includes a temperature recorder 9 and a temperature measuring thermocouple 10;
[0050] In the casting module, the casting mold upper mold 2 is provided with a lifting structure, the casting mo...
PUM
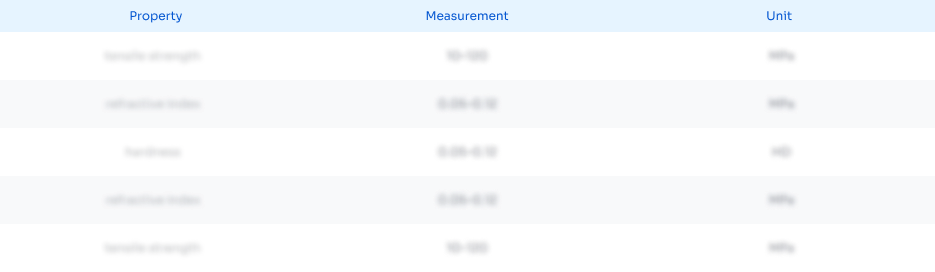
Abstract
Description
Claims
Application Information

- Generate Ideas
- Intellectual Property
- Life Sciences
- Materials
- Tech Scout
- Unparalleled Data Quality
- Higher Quality Content
- 60% Fewer Hallucinations
Browse by: Latest US Patents, China's latest patents, Technical Efficacy Thesaurus, Application Domain, Technology Topic, Popular Technical Reports.
© 2025 PatSnap. All rights reserved.Legal|Privacy policy|Modern Slavery Act Transparency Statement|Sitemap|About US| Contact US: help@patsnap.com