Production process of 3D glass back cover plate of mobile phone
A production process and back cover technology, which is applied in the field of production technology of mobile phone 3D glass back cover, can solve the problem that the strength, wear resistance and heat resistance of the back cover are not ideal, the polishing defect rate is high, and the development is restricted. problem, to achieve the effect of shortening polishing time, saving yield and consistent thickness
- Summary
- Abstract
- Description
- Claims
- Application Information
AI Technical Summary
Problems solved by technology
Method used
Examples
Embodiment 1
[0020] The production process of a kind of mobile phone 3D glass rear cover that the present invention proposes comprises the following steps:
[0021] S1. Cutting the 3D glass raw material with a glass substrate cutting machine to obtain the base material;
[0022] S2. Put the base material into a graphite mold after CNC processing, and then perform hot bending forming on a hot press bending machine, and obtain a slab after cooling down;
[0023] S3, polishing the slab, and then performing tempering treatment to obtain a tempered slab;
[0024] S4. Screen printing LOGO on the toughened slab, spraying ink, and obtaining the 3D glass back cover of the mobile phone after drying.
Embodiment 2
[0026] The production process of a kind of mobile phone 3D glass rear cover that the present invention proposes comprises the following steps:
[0027] S1. Cutting the 3D glass raw material with a glass substrate cutting machine to obtain the base material;
[0028] S2. Put the base material into a graphite mold after CNC processing, and then perform hot bending forming on a hot press bending machine, and obtain a slab after cooling down;
[0029] S3, polishing the slab, and then performing tempering treatment to obtain a tempered slab;
[0030] S4, screen printing LOGO on the toughened slab, spraying ink, and obtaining the 3D glass back cover of the mobile phone after drying;
[0031] Among them, in S2, in the process of hot press bending, the temperature inside the hot press brake is 750 ° C, and the time is 25 minutes; there are 15 stations in the hot press brake, of which 7 preheating stations , 3 molding stations, 5 cooling stations;
[0032] In S3, the polishing inclu...
Embodiment 3
[0040] The production process of a kind of mobile phone 3D glass rear cover that the present invention proposes comprises the following steps:
[0041] S1. Cutting the 3D glass raw material with a glass substrate cutting machine to obtain the base material;
[0042] S2. Put the base material into a graphite mold after CNC processing, and then perform hot bending forming on a hot press bending machine, and obtain a slab after cooling down;
[0043] S3, polishing the slab, and then performing tempering treatment to obtain a tempered slab;
[0044] S4, screen printing LOGO on the toughened slab, spraying ink, and obtaining the 3D glass back cover of the mobile phone after drying;
[0045] Among them, in S2, during the process of hot press bending, the temperature inside the hot press brake is 720°C, and the time is 35 minutes; there are 15 stations in the hot press brake, of which 7 are preheating stations , 3 molding stations, 5 cooling stations;
[0046] In S3, the polishing...
PUM
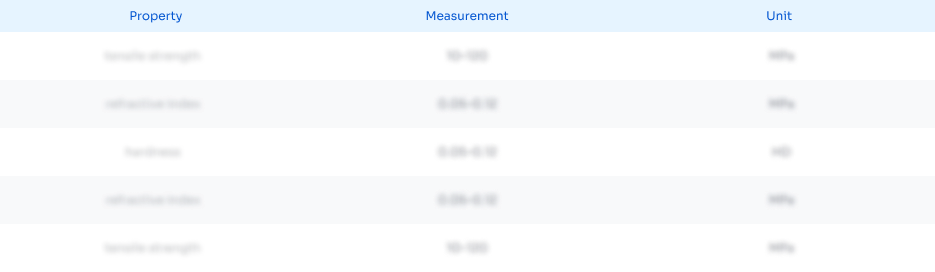
Abstract
Description
Claims
Application Information

- Generate Ideas
- Intellectual Property
- Life Sciences
- Materials
- Tech Scout
- Unparalleled Data Quality
- Higher Quality Content
- 60% Fewer Hallucinations
Browse by: Latest US Patents, China's latest patents, Technical Efficacy Thesaurus, Application Domain, Technology Topic, Popular Technical Reports.
© 2025 PatSnap. All rights reserved.Legal|Privacy policy|Modern Slavery Act Transparency Statement|Sitemap|About US| Contact US: help@patsnap.com