Ceramic grinding aid for ceramics grinding aluminate cement and manufacturing method thereof
A kind of technology of aluminate cement and grinding aid, which is applied in the field of ceramic grinding, can solve problems such as unbalanced, non-compact structure, and low ball milling efficiency, and achieve improved weather resistance and acid and alkali resistance, excellent quick-drying performance, dry excellent rigidity
- Summary
- Abstract
- Description
- Claims
- Application Information
AI Technical Summary
Problems solved by technology
Method used
Examples
Embodiment 1
[0018] A ceramic grinding aid for grinding aluminate cement ceramics, the ceramic grinding aid is composed of three components, wherein component A is 18g of wheat bran powder in parts by weight, 0.3g of collagen activating enzyme water, 18g of dry straw powder, 0.3g of cellulophage bacterial agent are mixed and fermented for 20h to obtain the pre-fermentation product; component B is 150g of sodium silicate solute containing 10% sodium silicate solute aqueous solution 150g, pine bark 3g, oxidation Calcium 2.4g, the foaming product obtained after 3-5 days of foaming; component C is 10g of hard grinding aid silicon dioxide.
[0019] The manufacture method of above-mentioned ceramic grinding aid, comprises the following steps:
[0020] 1) Raw material preparation
[0021] 1. Raw material preparation: Prepare 150g of sodium silicate solute 10% aqueous solution of sodium silicate, 18g of wheat bran powder, 3g of pine bark, 10g of silicon dioxide powder, 0.3g of collagen activating...
Embodiment 2
[0029] A ceramic grinding aid for grinding aluminate cement ceramics, the ceramic grinding aid is composed of three components, wherein component A is 15g of wheat bran powder in parts by weight, 0.2g of collagen activating enzyme water, Dry straw powder 15, 0.2 g of cellulophage bacterial agent are mixed and fermented for 18 hours to obtain a pre-fermented product; component B is 180 g of sodium silicate solute containing 10% sodium silicate solute aqueous solution 180 g, pine bark 2 g, oxidized Calcium 2.2g, the foamed product obtained after 3 days of foaming; component C is 8g of hard grinding aid silicon dioxide.
[0030] The manufacture method of above-mentioned ceramic grinding aid, comprises the following steps:
[0031] 1) Raw material preparation
[0032] 1. raw material preparation: prepare 180g of sodium silicate solute 10% sodium silicate aqueous solution, 15g of wheat bran powder, 2g of pine bark, 8g of silicon dioxide powder, 0.2g of collagen activating enzyme w...
PUM
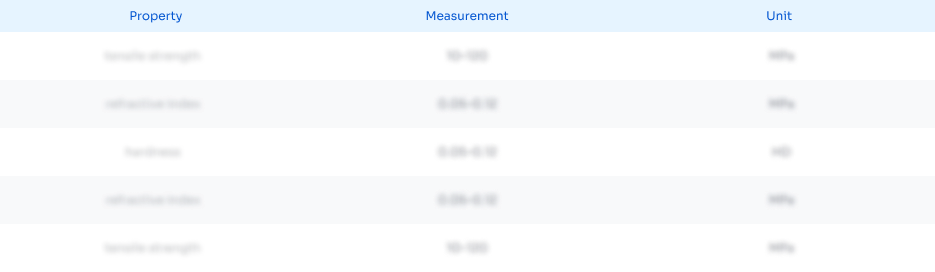
Abstract
Description
Claims
Application Information

- R&D
- Intellectual Property
- Life Sciences
- Materials
- Tech Scout
- Unparalleled Data Quality
- Higher Quality Content
- 60% Fewer Hallucinations
Browse by: Latest US Patents, China's latest patents, Technical Efficacy Thesaurus, Application Domain, Technology Topic, Popular Technical Reports.
© 2025 PatSnap. All rights reserved.Legal|Privacy policy|Modern Slavery Act Transparency Statement|Sitemap|About US| Contact US: help@patsnap.com