Automatic feeding position tracking control method of numerical control cutting machining process
A processing and automatic feeding technology, applied in metal processing, electrical digital data processing, special data processing applications, etc., can solve the problems of low accuracy, poor real-time performance, poor speed, etc., and achieve simple online implementation, simple design and practicality strong effect
- Summary
- Abstract
- Description
- Claims
- Application Information
AI Technical Summary
Problems solved by technology
Method used
Image
Examples
Embodiment Construction
[0028] The method of the present invention will be described in further detail below in conjunction with the accompanying drawings.
[0029] refer to figure 1 , figure 2 with image 3 , a method for tracking and controlling automatic feeding positions in a numerically controlled cutting process, said method comprising the steps of:
[0030] 1) Consider the second-order continuous-time dynamic mathematical model of the displacement and torque of the raw material conveyor belt during the CNC cutting process, see formula (1):
[0031]
[0032] Among them, t represents the time variable, s; x 1 Indicates the displacement variable of the conveyor belt, that is, the feeding position, m; x 2 Indicates the feeding speed of the conveyor belt, m / s; "·" indicates the first derivative of the corresponding variable; the constant C is the damping coefficient, N s / m; M is the mass of the raw material, kg; the constant H is the lead of the transmission device , m; the constant J is t...
PUM
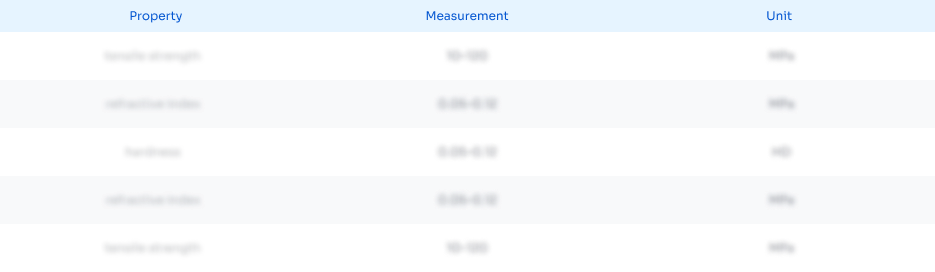
Abstract
Description
Claims
Application Information

- R&D Engineer
- R&D Manager
- IP Professional
- Industry Leading Data Capabilities
- Powerful AI technology
- Patent DNA Extraction
Browse by: Latest US Patents, China's latest patents, Technical Efficacy Thesaurus, Application Domain, Technology Topic, Popular Technical Reports.
© 2024 PatSnap. All rights reserved.Legal|Privacy policy|Modern Slavery Act Transparency Statement|Sitemap|About US| Contact US: help@patsnap.com